Introduction
Relays are essential components in electrical and electronic systems, serving as switches that control high-power circuits using low-power signals. They play a crucial role in automating processes and ensuring safety in various applications, from household appliances to industrial machinery. This article explores the different types of relays, their working principles, and their applications across various fields.
Basic Working Principle of a Relay
A relay operates as an electromagnetic switch. When a small voltage is applied to the coil of the relay, it generates a magnetic field that moves an armature. This movement either opens or closes contacts, allowing or interrupting the flow of electricity through a circuit.
Key Components
- Coil: The wire wound around a core that generates a magnetic field when energized.
- Armature: A movable component that is attracted by the magnetic field created by the coil.
- Contacts: The conductive parts that open or close the circuit when the armature moves.
A simplified diagram illustrating relay operation would show these components and their interactions during activation.
Types of Relays
3.1 Electromechanical Relays (EMR)
Construction and Working:
Electromechanical relays consist of an electromagnetic coil, armature, and contacts. When current flows through the coil, it generates a magnetic field that pulls the armature towards it, closing the contacts.
Advantages:
- Simplicity in design
- High reliability
- Electrical isolation between control and load circuits
Disadvantages:
- Mechanical wear over time
- Slower response times compared to solid-state relays
Applications:
Commonly used in industrial automation, home appliances, and automotive systems for switching operations.
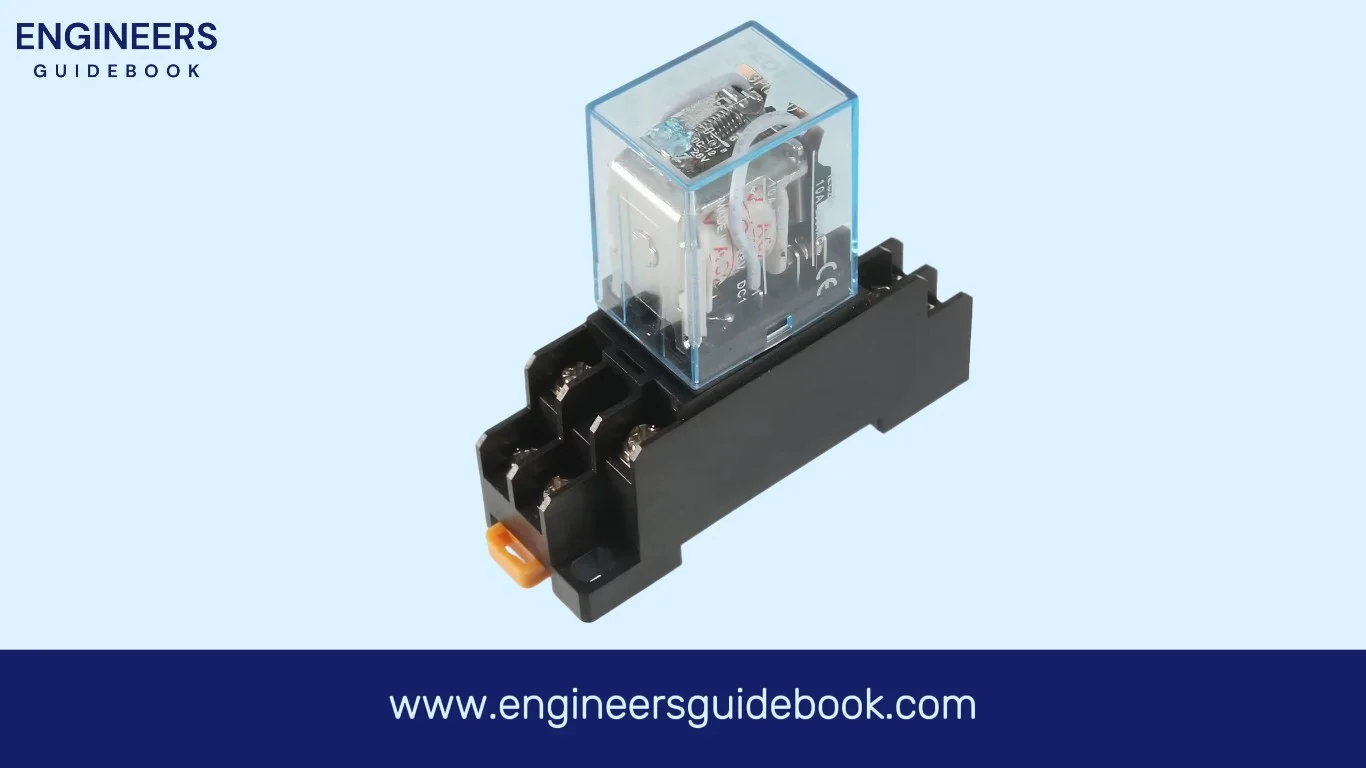
3.2 Solid State Relays (SSR)
Construction and Working:
Solid state relays use semiconductor devices such as transistors or thyristors instead of mechanical moving parts. They operate by controlling the flow of current through these semiconductor devices when a voltage is applied.
Advantages:
- High-speed operation
- Longer lifespan due to no mechanical parts
- No contact bounce
Disadvantages:
- Heat dissipation can be an issue
- Generally more expensive than EMRs
Applications:
Ideal for high-speed switching tasks, noise-sensitive environments, and medical equipment where reliability is crucial.
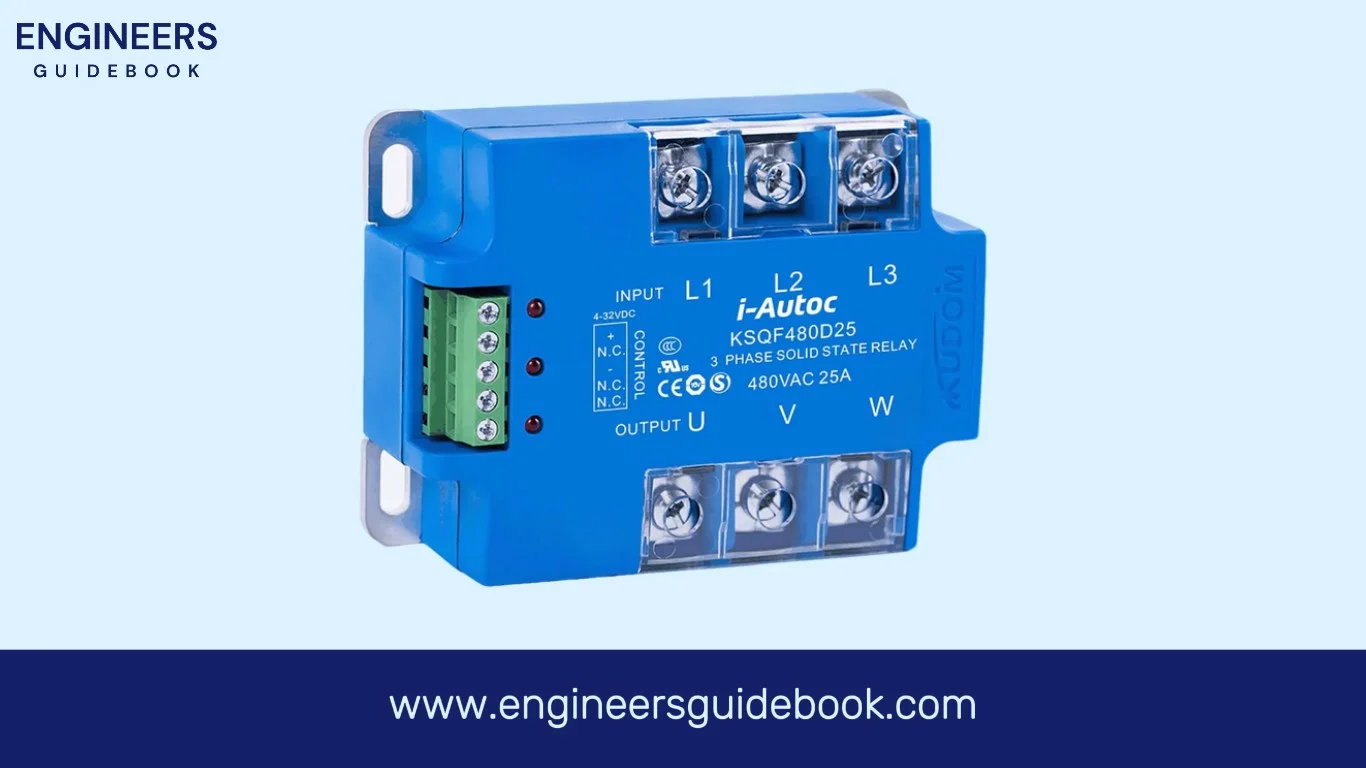
3.3 Reed Relays
Construction and Working:
Reed relays utilize reed switches encased in a glass tube. When exposed to a magnetic field, the reeds close together to complete an electrical circuit.
Advantages:
- Compact size
- Fast switching speeds
- Low power consumption
Disadvantages:
- Limited switching capacity
- Fragile construction
Applications:
Widely used in telecommunications, instrumentation, and medical devices where space is limited and quick response times are necessary.
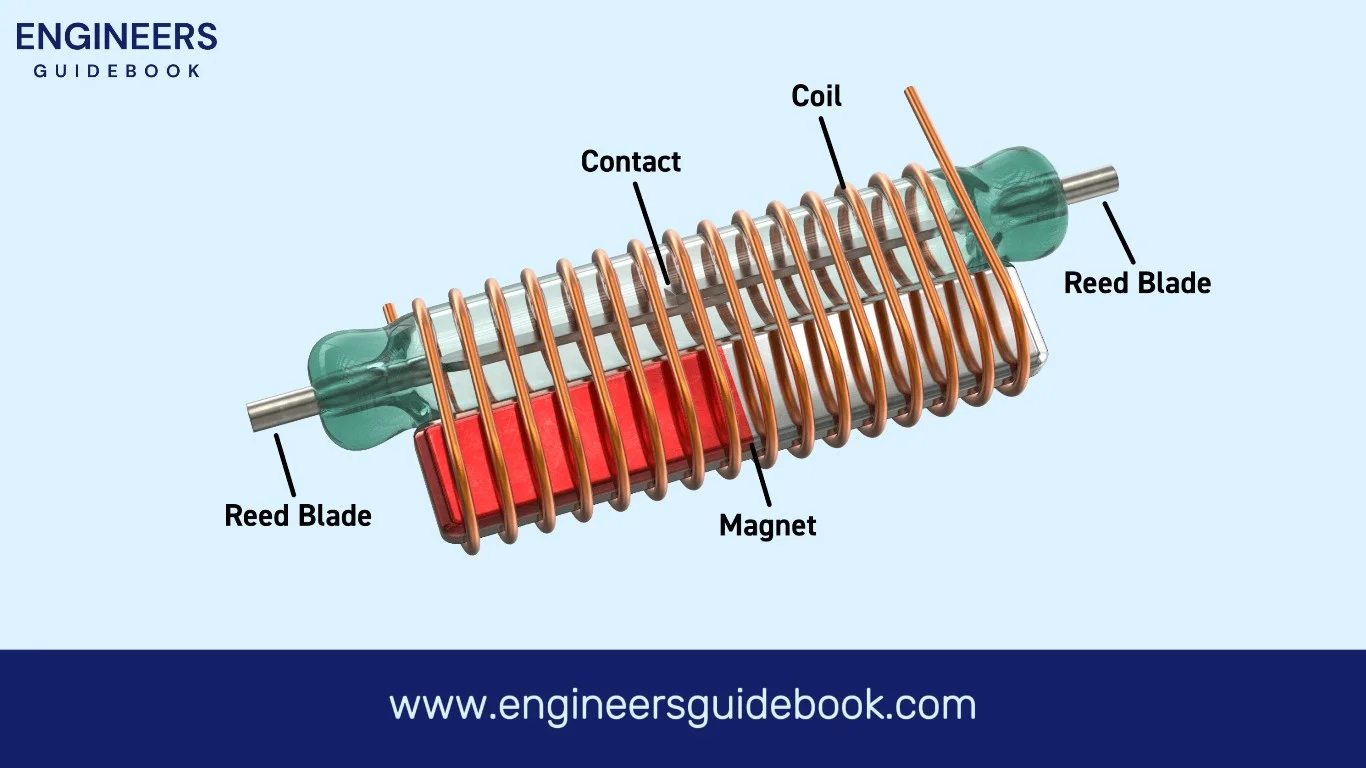
3.4 Thermal Relays
Construction and Working:
These relays operate using bimetallic strips that bend when heated. This bending action opens or closes contacts based on temperature changes.
Advantages:
- Simple design
- Provides overload protection
Disadvantages:
- Slow response times
- Limited precision in temperature control
Applications:
Commonly found in motor protection circuits and heating systems to prevent overheating.
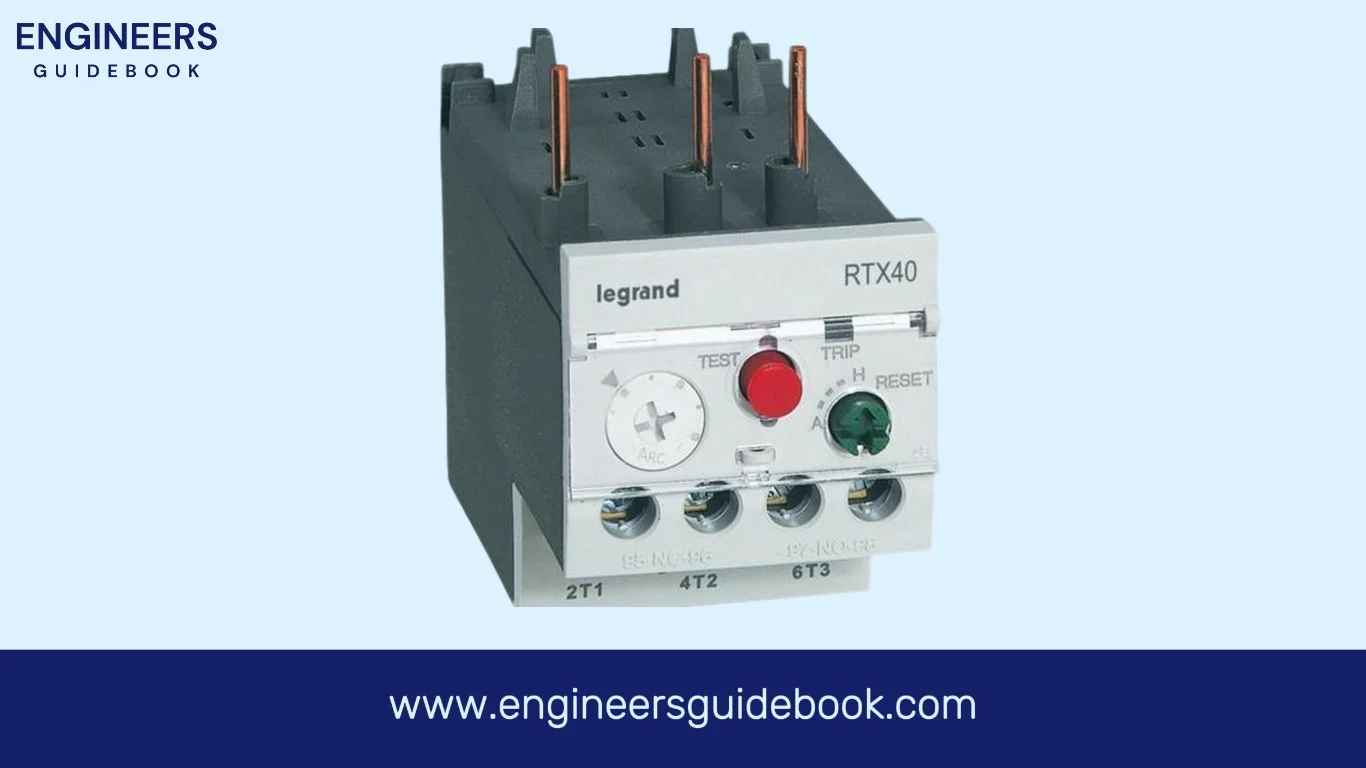
3.5 Time Delay Relays
Construction and Working:
Time delay relays introduce a predetermined delay before switching occurs. They can be mechanical or electronic in design.
Advantages:
- Precise timing control
- Versatile applications in automation
Disadvantages:
- More complex than standard relays
- Potential for failure over time due to component aging
Applications:
Used in industrial control systems, HVAC systems for delayed fan start-up, and lighting control systems.
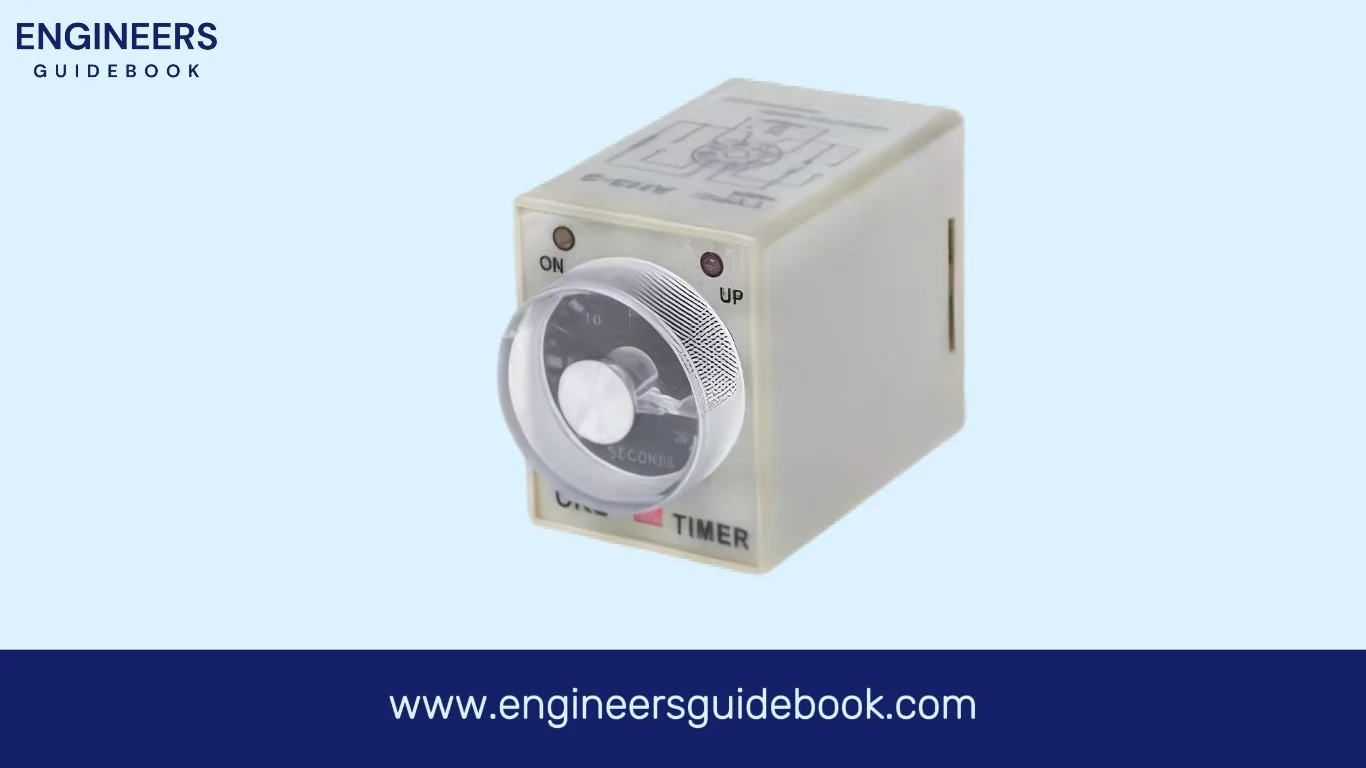
3.6 Latching Relays
Construction and Working:
Latching relays maintain their state after being activated without a continuous power supply. They can be reset by applying a second pulse.
Advantages:
- Energy efficient as they do not require constant power
- Can hold their state indefinitely until reset
Disadvantages:
- More complex reset mechanisms
- May require specific pulse sequences for operation
Applications:
Utilized in memory circuits, energy-saving systems, and remote controls where maintaining state is beneficial.
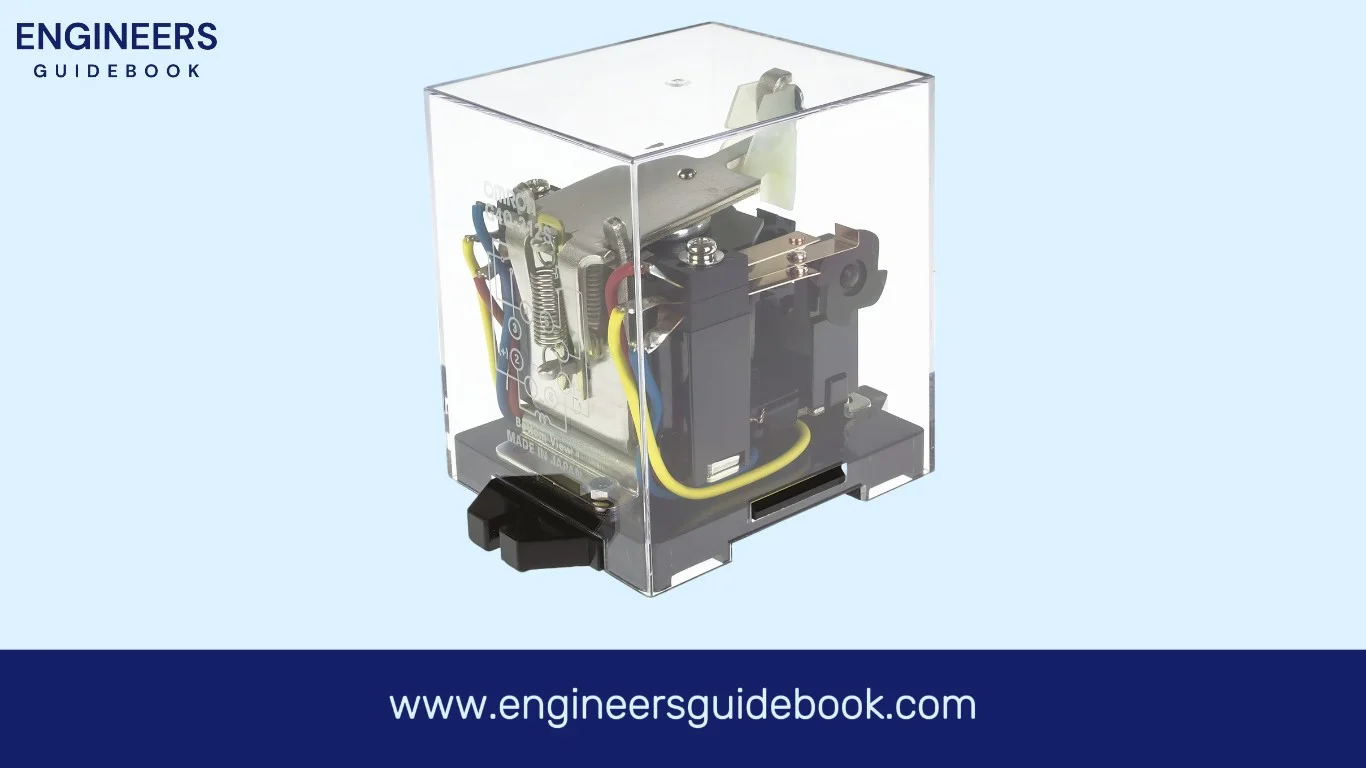
3.7 Hybrid Relays
Construction and Working:
Hybrid relays combine features of both electromechanical and solid-state technologies to leverage the advantages of both types.
Advantages:
- Improved durability compared to traditional EMRs
- Enhanced performance due to solid-state components
- Higher cost than standard relays
- Increased complexity in design and application
Disadvantages:
Applications:
Suitable for high-power applications or environments with frequent switching demands where reliability is critical.
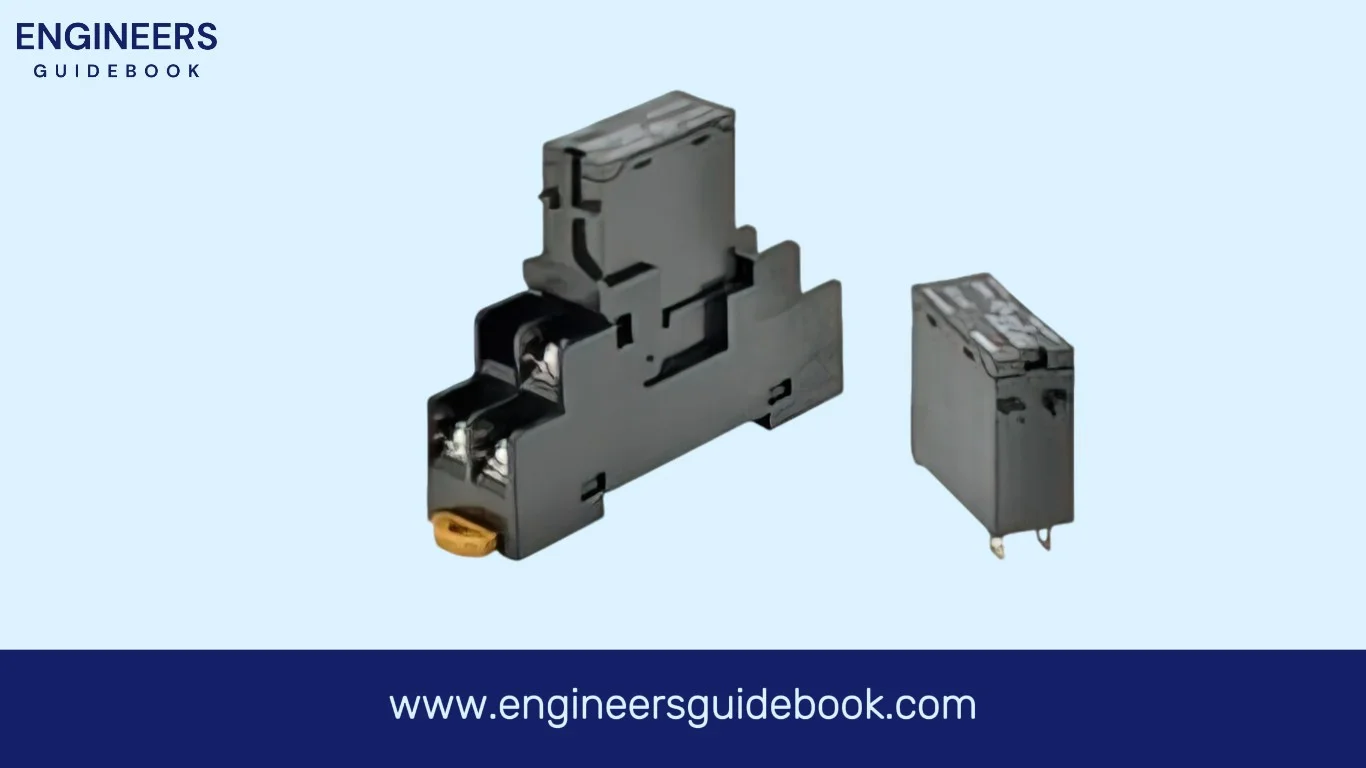
Relay Specifications and Selection Criteria
When selecting a relay for specific applications, several specifications must be considered:
- Load Voltage and Current Ratings: Ensure the relay can handle the voltage and current requirements of the application.
- Coil Voltage: The voltage required to activate the relay’s coil.
- Contact Configuration: Common configurations include SPST (Single Pole Single Throw), SPDT (Single Pole Double Throw), DPDT (Double Pole Double Throw), etc.
- Operating Time and Release Time: The time it takes for the relay to switch on/off.
- Environmental Considerations: Factors like temperature range, humidity levels, and exposure to dust or chemicals can affect relay performance.
- Mechanical and Electrical Life Expectancy: The expected lifespan of the relay under normal operating conditions.
Common Applications of Relays
Relays find applications across numerous fields:
- Industrial Automation: Used for controlling machinery operations, safety interlocks, and process automation.
- Home Automation: Implemented in lighting control systems, security alarms, and smart home devices.
- Automotive Systems: Control functions such as fuel pump operation, headlight switching, and other electrical systems within vehicles.
- Telecommunications: Employed for signal routing, line protection, and network management tasks.
- Power Systems: Critical for circuit protection mechanisms, load shedding during peak demands, and system monitoring.
Advantages and Limitations of Using Relays
Relays offer numerous benefits but also come with limitations:
Advantages:
- Provide electrical isolation between control circuits and high-power loads.
- Enable remote control of electrical devices.
- Enhance safety by preventing overloads through protective mechanisms.
Limitations:
- Mechanical wear can lead to failure over time in electromechanical relays.
- Solid-state relays may experience thermal issues if not properly managed.
- Some relay types may have slower response times compared to direct electronic switching methods.
Emerging Trends and Technologies in Relays
The field of relays is evolving with new technologies:
Smart Relays:
Integration with IoT (Internet of Things) allows for remote monitoring and control capabilities within smart grids.
Miniaturization:
Development of micro-relays enables their use in compact electronic devices without compromising performance.
Energy Efficiency:
Focus on low-power relays helps reduce energy consumption across various applications while maintaining functionality.
Conclusion
In summary, understanding the different types of relays—along with their working principles—helps engineers select appropriate solutions for specific applications. The importance of choosing the right relay cannot be overstated; it directly impacts system reliability, efficiency, and safety across various sectors from industrial automation to consumer electronics.
FAQ Section
10.1 What is the main function of a relay?
Relays control high-power circuits using low-power signals by acting as an electrically operated switch that opens or closes contacts based on input signals.
10.2 How do I choose the right relay for my application?
Key factors include voltage ratings (both load voltage and coil voltage), current ratings, contact configuration (such as SPST or DPDT), environmental conditions (like temperature), operating time requirements, and expected lifespan under normal use conditions.
10.3 What is the difference between electromechanical and solid state relays?
Electromechanical relays utilize physical moving parts (coil/armature) while solid-state relays use semiconductor materials for switching operations; this results in differences in speed, lifespan, cost, heat generation, and reliability under varying conditions.
10.4 Can a relay be used in both AC and DC circuits?
Yes! However, specific considerations must be taken into account regarding contact ratings since some relays are designed explicitly for AC or DC applications due to differences in how they handle voltage spikes during switching operations.
10.5 What are some common signs of relay failure?
Common symptoms include failure to switch on/off when commanded; erratic behavior such as intermittent operation; excessive heat generation; visible damage like burned contacts; or unusual noises during operation which may indicate mechanical wear or electrical faults within the device itself.
10.6 How do smart relays differ from traditional relays?
Smart relays incorporate advanced features such as connectivity options (like Wi-Fi or Bluetooth) enabling integration with IoT systems; they often provide enhanced monitoring capabilities allowing users real-time insights into performance metrics compared to traditional models which operate solely based on physical inputs without feedback mechanisms integrated into their design.