1. Introduction
Electric motors serve as the backbone of industrial automation, consumer electronics, and transportation systems. Their ability to convert electrical energy into mechanical motion underpins countless applications, from manufacturing machinery to household appliances and electric vehicles. As industries evolve towards efficiency and sustainability, the selection of the right motor type remains a pivotal consideration.
Why AC and DC Motors Matter in Engineering
The choice between alternating current (AC) and direct current (DC) motors determines performance efficiency, operational cost, and application suitability. AC motors dominate large-scale industrial applications due to their reliability and adaptability to variable-speed operations, while DC motors excel in precision-driven applications that require fine-tuned control over torque and speed.
Several fundamental distinctions exist between AC and DC motors, including power supply type, construction, efficiency, speed control, and maintenance requirements. Understanding these factors enables engineers and manufacturers to optimize motor selection for specific applications, balancing cost-effectiveness with performance.
2. Fundamentals of Electric Motors
2.1 What Is an Electric Motor?
An electric motor is an electromechanical device that converts electrical energy into mechanical energy through electromagnetic interactions. By utilizing a rotating magnetic field, these motors generate torque, facilitating movement in various mechanical systems.
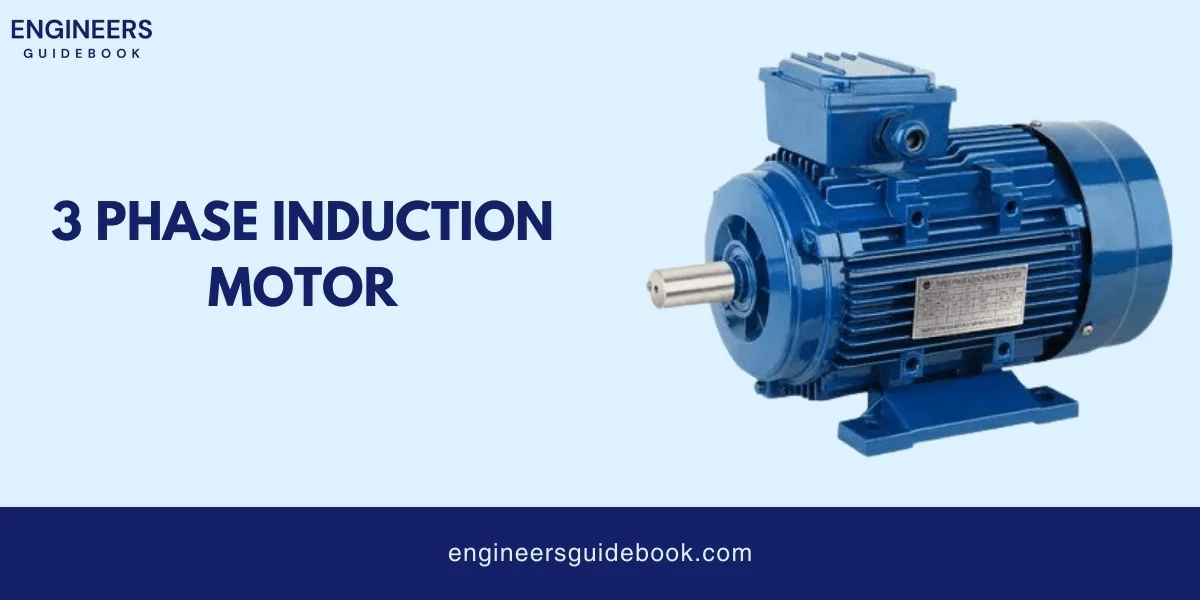
2.2 Basic Principles of Electromagnetic Induction
The operational mechanism of most electric motors is based on electromagnetic induction, as described by Faraday’s Law. When an electric current passes through a conductor in a magnetic field, a force is exerted on the conductor, generating rotational motion. This principle forms the foundation for both AC and DC motor operations, albeit with distinct methodologies in execution.
2.3 The Importance of Electric Motors in Industrial Applications
Industries rely on electric motors for automation, energy efficiency, and enhanced productivity. They power conveyor belts, pumps, compressors, robotics, and HVAC systems, enabling seamless industrial operations. The integration of variable speed drives and smart motor technologies further augments efficiency, making electric motors indispensable in modern engineering solutions.
3. Overview of AC Motors
3.1 What Is an AC Motor?
An AC motor operates using alternating current, which periodically reverses direction. This motor type is widely used in industrial and commercial settings due to its robustness, scalability, and ability to function over extended periods with minimal maintenance.
3.2 Basic Working Principle of AC Motors
AC motors function by generating a rotating magnetic field in the stator, inducing a current in the rotor that produces motion. The rotation speed depends on the supply frequency and the motor’s pole count, making frequency control essential for speed modulation.
3.3 Types of AC Motors
3.3.1 Induction Motors (Asynchronous Motors)
Induction motors are the most common type of AC motors. They operate based on electromagnetic induction, where the rotor current is induced by the stator’s rotating magnetic field. These motors are widely used due to their ruggedness, low maintenance, and cost-effectiveness.
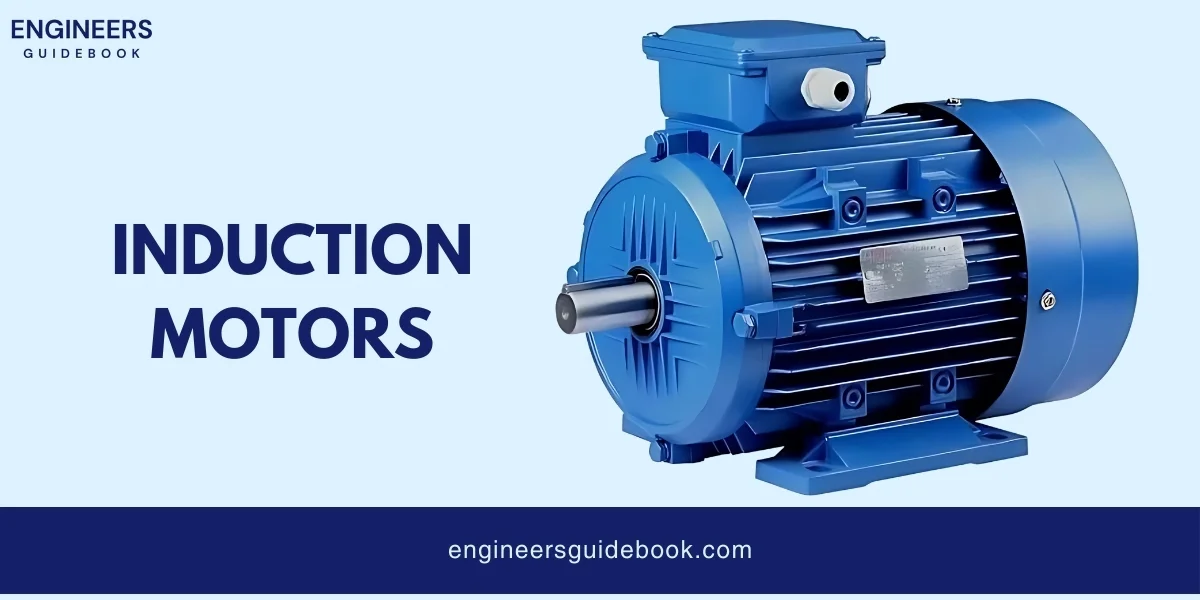
3.3.2 Synchronous Motors
Synchronous motors operate at a constant speed dictated by the supply frequency. Unlike induction motors, they require an external excitation source to synchronize the rotor with the stator’s magnetic field. They are preferred for precision applications such as clocks, conveyors, and power factor correction systems.
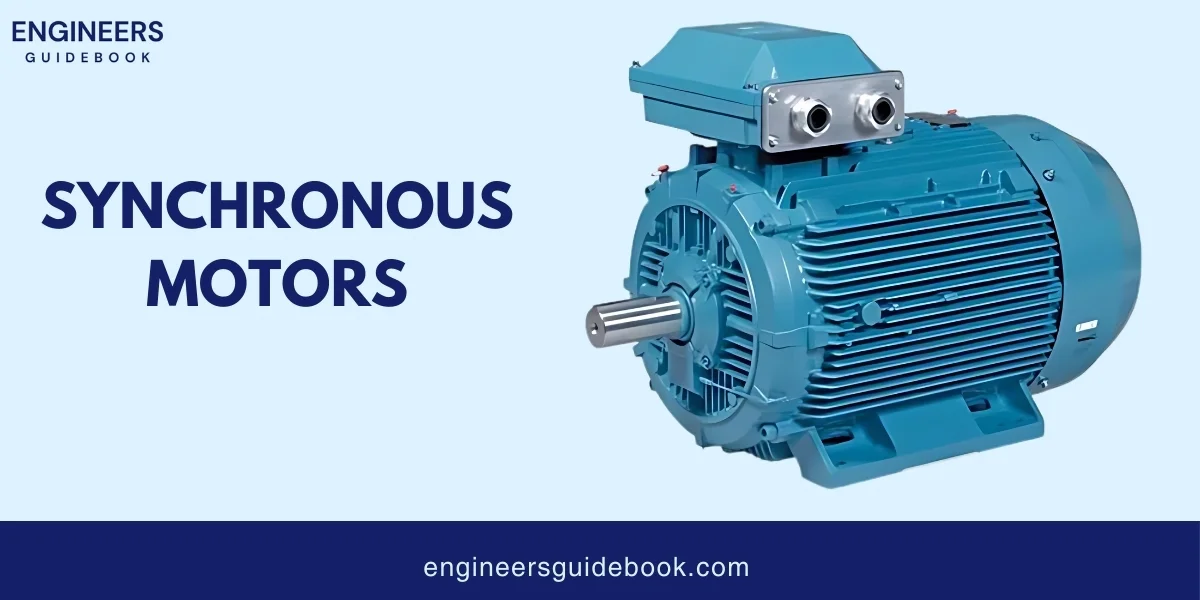
3.4 Key Components of AC Motors
3.4.1 Stator and Rotor
The stator is the stationary part that generates the magnetic field, while the rotor is the rotating component that interacts with this field to produce motion.
3.4.2 Windings and Magnetic Field Generation
The stator windings carry the AC supply, generating the magnetic field that drives the rotor. The arrangement of windings influences motor efficiency and performance characteristics.
3.4.3 Power Supply and Frequency Dependency
AC motors rely on a steady alternating current supply. The frequency of the supply determines the motor’s operating speed, which can be controlled using frequency inverters for variable-speed applications.
4. Overview of DC Motors
4.1 What Is a DC Motor?
A DC motor operates using direct current, where the electric charge flows in a single direction. These motors provide excellent speed control and high starting torque, making them suitable for applications requiring precision movement.
4.2 Basic Working Principle of DC Motors
DC motors function through the interaction of a magnetic field and a current-carrying conductor. The commutator and brushes facilitate continuous rotation by reversing the current direction at appropriate intervals, ensuring sustained motion.
4.3 Types of DC Motors
4.3.1 Brushed DC Motors
Brushed DC motors utilize carbon brushes and a commutator to regulate current flow within the rotor windings. While simple and cost-effective, these motors require regular maintenance due to brush wear.
4.3.2 Brushless DC Motors
Brushless DC (BLDC) motors eliminate the need for brushes and a commutator, relying on electronic controllers to manage current flow. These motors offer higher efficiency, reduced maintenance, and improved durability compared to their brushed counterparts.
4.3.3 Series, Shunt, and Compound DC Motors
- Series DC Motors: Provide high starting torque, making them ideal for traction and lifting applications.
- Shunt DC Motors: Offer stable speed control, suitable for applications like lathes and pumps.
- Compound DC Motors: Combine characteristics of series and shunt motors, balancing torque and speed stability.
4.4 Key Components of DC Motors
4.4.1 Armature and Commutator
The armature is the rotating component, while the commutator ensures current direction reversal to maintain rotation.
4.4.2 Brushes and Electrical Connections
Brushed motors use carbon brushes to transmit electricity to the rotating commutator, facilitating consistent operation.
4.4.3 Permanent Magnets vs. Electromagnets
DC motors can incorporate permanent magnets for efficiency or electromagnets for adjustable magnetic field strength, impacting performance characteristics based on the application.
5. Key Differences Between AC and DC Motors
5.1 Power Supply: Alternating vs. Direct Current AC (Alternating Current) motors operate on electrical energy where current periodically reverses direction. This fluctuating current facilitates efficient long-distance power transmission.
5.2 Construction and Design Variations AC motors typically comprise a stator (stationary part) and a rotor (rotating part), functioning through electromagnetic induction. These motors are further categorized into synchronous and asynchronous types. DC motors feature a commutator, brushes, and an armature winding, enabling direct conversion of electrical energy into mechanical rotation.
5.3 Working Mechanism: Magnetic Field Differences AC motors generate rotating magnetic fields through alternating current cycles, inducing current in the rotor via electromagnetic principles. DC motors rely on a static magnetic field with direct current input, facilitating controlled rotation based on polarity shifts.
5.4 Speed Control: Efficiency and Performance AC motors require frequency control via variable frequency drives (VFDs) for speed modulation, making their control systems complex yet highly efficient. In contrast, DC motors achieve speed variation through voltage adjustments, offering superior precision with simpler electronic controllers, advantageous in automation and robotics.
5.5 Maintenance Requirements: Wear and Tear Factors AC motors, especially induction variants, exhibit low maintenance demands due to their brushless design. Conversely, brushed DC motors necessitate regular maintenance due to brush and commutator wear. However, brushless DC motors mitigate this issue, bridging the gap between AC and traditional DC motor designs.
5.6 Cost Considerations: Initial Investment vs. Long-Term Expenses AC motors generally have a higher initial cost due to intricate control requirements, particularly for applications demanding speed regulation. Nonetheless, their longevity and minimal maintenance often result in lower lifecycle costs. DC motors, with their simpler controllers, may present lower upfront costs but can incur greater long-term expenses due to wear-prone components.
6. Efficiency and Performance Comparison
6.1 Power Consumption and Energy Efficiency AC motors, especially synchronous variants, exhibit superior energy efficiency in large-scale industrial applications. DC motors, while efficient in localized applications, often experience losses due to resistive heating in brushes and windings.
6.2 Torque and Speed Characteristics DC motors provide high starting torque, making them suitable for applications requiring immediate load response. AC motors, particularly induction types, exhibit a more gradual torque buildup, advantageous for continuous, high-power operations.
6.3 Load Handling Capabilities AC motors excel in handling fluctuating loads in industrial environments, whereas DC motors are optimal for controlled-load applications. The robust design of AC motors enables them to sustain prolonged operations under varying torque demands.
6.4 Response Time and Dynamic Performance DC motors offer faster response times due to direct voltage control, critical for applications necessitating rapid adjustments. AC motors, reliant on frequency alterations, demonstrate a slightly delayed but stable response suited for long-term efficiency.
7. Applications of AC Motors
7.1 Industrial Applications: AC motors dominate industrial sectors, driving pumps, compressors, conveyors, and large-scale manufacturing equipment due to their durability and efficiency.
7.2 Home Appliances: Household devices such as refrigerators, washing machines, and air conditioners employ AC motors for reliable and continuous operation.
7.3 Transportation Sector: Electric trains, elevators, and centralized HVAC systems rely on AC motors for their efficiency in sustained power delivery and smooth performance.
7.4 Renewable Energy: Wind turbines and hydroelectric generators incorporate AC motors due to their compatibility with grid systems and ability to handle variable loads.
8. Applications of DC Motors
8.1 Automotive Industry: DC motors, particularly brushless types, power electric vehicles (EVs) due to their high efficiency and torque control capabilities.
8.2 Robotics and Automation: Automated machinery and robotic arms utilize DC motors for their fine-tuned motion control, ensuring precision in industrial and research applications.
8.3 Consumer Electronics: From computer fans to electric toothbrushes, DC motors are indispensable in consumer electronics requiring compact, efficient operation.
8.4 Medical Equipment: DC motors drive critical medical devices such as infusion pumps, ventilators, and prosthetic limbs, where precise motion control is vital.
9. Advantages and Disadvantages of AC Motors
9.1 Advantages of AC Motors
- With fewer wear-prone components, AC motors ensure longevity and reduced maintenance.
- AC motors provide efficient power delivery, making them economical for industrial-scale use.
- Seamless integration into power grids allows for stable and continuous operation.
9.2 Disadvantages of AC Motors
- Regulating AC motor speed necessitates sophisticated controllers, increasing system complexity.
- Advanced speed control mechanisms and installation requirements elevate initial expenses.
10. Advantages and Disadvantages of DC Motors
10.1 Advantages of DC Motors
- DC motors offer exceptional speed regulation through voltage adjustments, allowing for seamless transitions and precise control in automation and robotics.
- These motors excel in applications demanding significant initial torque, such as electric vehicles and industrial machinery.
- DC motors feature a straightforward design with minimal control requirements, making them well-suited for compact systems like household appliances and battery-powered devices.
10.2 Disadvantages of DC Motors
- Wear-prone components necessitate periodic maintenance, increasing long-term costs.
- Scalability constraints make DC motors less viable for high-power applications.
11. Conclusion
AC motors are preferred for large-scale and energy-efficient applications due to their robust design and ability to handle variable loads. Conversely, DC motors offer superior control, making them ideal for applications requiring precise speed and torque regulation.
The selection of AC or DC motors depends on operational requirements such as efficiency, control complexity, and cost. While AC motors are more suited for continuous and high-power operations, DC motors excel in environments requiring rapid response and adaptability.
12. FAQS
1. What is the fundamental difference between AC and DC motors?
AC motors operate using alternating current, where the flow of electricity periodically reverses direction, while DC motors use direct current, where electricity flows in a single direction. This distinction affects their efficiency, speed control, and applications.
2. Which motor type is more energy-efficient?
AC motors, especially synchronous ones, tend to be more energy-efficient for high-power industrial applications due to their ability to operate at a constant speed with minimal energy loss. DC motors, however, offer efficiency in small-scale applications with precise control.
3. Why are AC motors commonly used in industrial applications?
AC motors are preferred in industrial settings because they are durable, require less maintenance, and can handle high-power loads efficiently. Their compatibility with grid power and ability to function with minimal wear make them ideal for heavy-duty use.
4. What are the main advantages of DC motors?
DC motors provide excellent speed control, high starting torque, and smooth operation, making them ideal for applications like robotics, electric vehicles, and consumer electronics. Brushless DC motors further improve efficiency and lifespan.
5. How do AC and DC motors differ in maintenance requirements?
AC motors, especially induction types, require less maintenance since they do not have brushes or commutators. In contrast, brushed DC motors require periodic maintenance due to brush wear, although brushless DC motors mitigate this issue.
6. Which motor type is better for electric vehicles (EVs)?
DC motors, particularly brushless DC (BLDC) motors, are widely used in electric vehicles because they offer high efficiency, better speed control, and rapid torque response, which are crucial for smooth driving performance.
7. Can AC motors be used in battery-powered applications?
AC motors can be used in battery-powered systems but typically require an inverter to convert DC from the battery to AC. This increases complexity and cost, which is why DC motors are more common in such applications.
8. What are the future trends in AC and DC motor technology?
Future advancements in electric motors include improved efficiency through AI-driven control systems, better materials for reduced energy loss, and greater integration with renewable energy systems, enhancing overall sustainability and performance.
One Response
love your article can you write mote on this topic.