1. Introduction
1.1 What Is Total Productive Maintenance (TPM)?
Total Productive Maintenance (TPM) is a holistic approach to equipment maintenance that strives to achieve perfect production processes by minimizing breakdowns, defects, and accidents. Unlike traditional maintenance methods that emphasize reactive responses to issues, TPM integrates maintenance into daily operations, making it a shared responsibility across all levels of the organization. By focusing on proactive and preventive measures, TPM ensures that machinery operates at its peak performance, thus fostering operational excellence.
1.2 The Origin and Evolution of TPM
The concept of TPM originated in Japan during the 1960s, spearheaded by the Nippon Denso company, a subsidiary of Toyota. Initially introduced as a strategy to improve equipment reliability, it quickly evolved into a comprehensive framework that integrates maintenance with quality and productivity. Over the decades, TPM principles have been adopted globally, transcending industries and becoming a cornerstone of lean manufacturing practices.
1.3 Why TPM Matters in Modern Industry
In today’s competitive industrial landscape, maximizing efficiency and minimizing waste are critical. TPM addresses these challenges by fostering a culture of continuous improvement and accountability. By reducing equipment downtime, ensuring consistent product quality, and promoting a safer work environment, TPM not only enhances operational efficiency but also contributes to long-term sustainability and profitability.
2. The Core Philosophy of TPM
2.1 Zero Breakdowns: A Paradigm Shift in Maintenance
The goal of zero breakdowns shifts the focus from reactive repairs to preventive maintenance. This philosophy emphasizes identifying potential issues before they escalate, ensuring uninterrupted operations and extending the lifespan of machinery. By eliminating breakdowns, organizations can achieve consistent production schedules and reduce associated costs.
2.2 Zero Defects: Ensuring Quality through Maintenance
Zero defects underscore the importance of equipment reliability in maintaining product quality. By addressing the root causes of defects—often linked to machinery inconsistencies—TPM ensures that every production cycle meets quality standards. This approach minimizes waste, rework, and customer dissatisfaction.
2.3 Zero Accidents: A Safety-First Approach
Safety is a foundational pillar of TPM. By incorporating regular inspections, proper training, and a culture of awareness, organizations can eliminate workplace accidents. This not only protects employees but also enhances productivity by fostering a secure and supportive work environment.
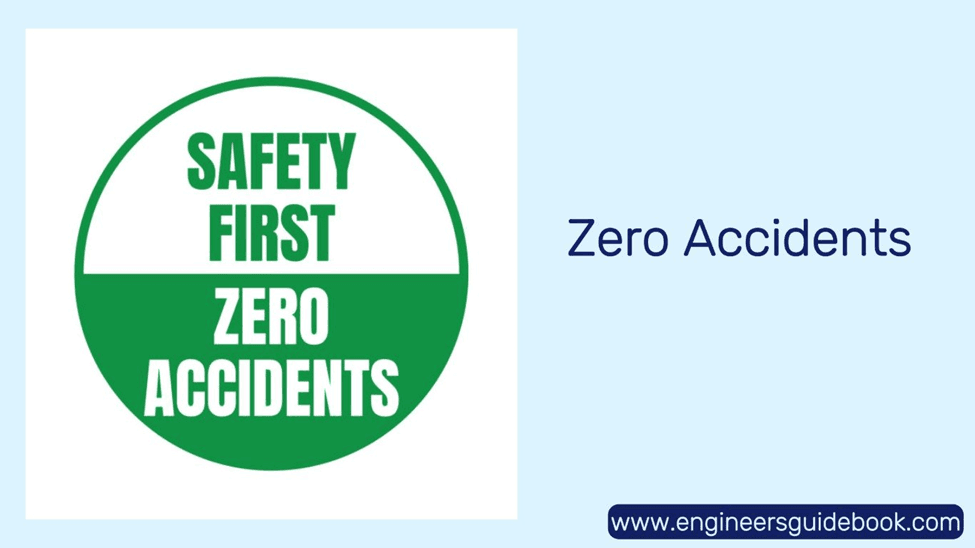
3. The Pillars of TPM
3.1 Autonomous Maintenance: Empowering Operators
Autonomous maintenance empowers machine operators to take ownership of routine maintenance tasks, such as cleaning, lubrication, and inspection. This reduces reliance on specialized technicians and ensures that minor issues are addressed promptly, preventing larger problems.
3.2 Planned Maintenance: Reducing Downtime through Scheduling
Planned maintenance involves systematic scheduling of maintenance activities based on historical data and equipment usage patterns. By predicting and addressing potential failures, organizations can minimize unplanned downtime and optimize resource utilization.
3.3 Quality Maintenance: Maintaining Standards with Precision
Quality maintenance focuses on identifying and eliminating factors that contribute to equipment-related defects. This involves meticulous attention to detail, thorough inspections, and adherence to strict maintenance protocols to ensure consistent product quality.
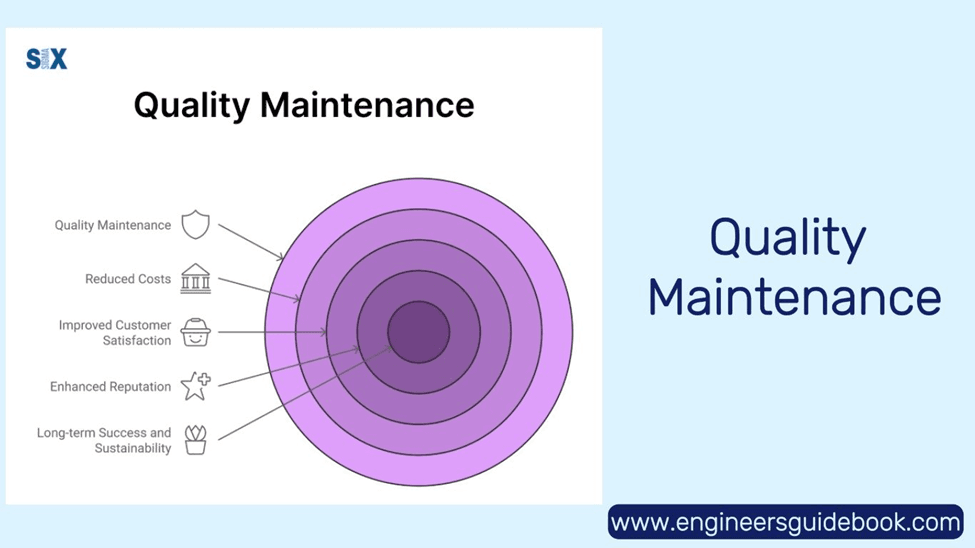
3.4 Focused Improvement: Driving Continuous Efficiency Gains
Focused improvement entails collaborative efforts to identify and eliminate inefficiencies in production processes. By engaging cross-functional teams in problem-solving initiatives, organizations can drive continuous improvement and achieve incremental gains in productivity.
3.5 Early Equipment Management: Designing for Reliability
Early equipment management integrates maintenance considerations into the design and procurement stages of machinery. By involving maintenance teams during equipment selection and installation, organizations can ensure that new machinery is reliable, easy to maintain, and aligned with operational goals.
3.6 Training and Education: Building a Skilled Workforce
A skilled and knowledgeable workforce is essential for successful TPM implementation. Comprehensive training programs equip employees with the technical expertise and problem-solving skills needed to maintain equipment effectively and contribute to continuous improvement initiatives.
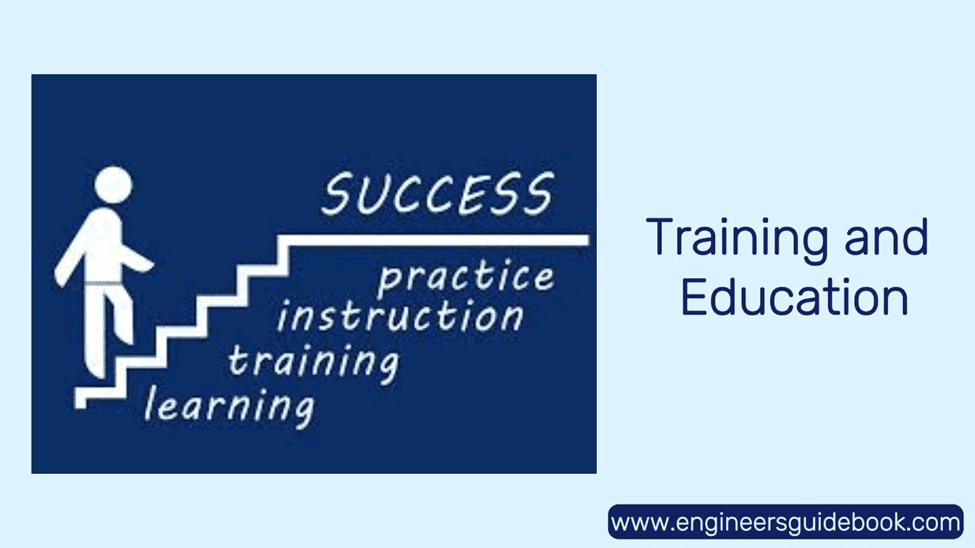
3.7 Safety, Health, and Environment: Beyond Compliance
TPM extends beyond compliance by fostering a proactive approach to safety, health, and environmental protection. This includes implementing safety protocols, reducing environmental impact, and promoting a culture of sustainability and well-being.
3.8 Office TPM: Extending Principles Beyond the Shop Floor
Office TPM applies TPM principles to administrative and support functions, streamlining processes and eliminating inefficiencies. By improving office workflows, organizations can enhance overall productivity and support seamless operations.
4. Key Components of TPM Implementation
4.1 Assessing the Current Maintenance Strategy
A comprehensive assessment of the existing maintenance strategy is the first step in TPM implementation. This involves identifying gaps, evaluating equipment performance, and understanding organizational readiness for change.
4.2 Establishing a TPM Steering Committee
A dedicated TPM steering committee provides leadership and direction for implementation efforts. Comprising representatives from various departments, the committee ensures alignment with organizational objectives and facilitates cross-functional collaboration.
4.3 Setting Clear and Measurable Goals
Clear and measurable goals provide a roadmap for TPM success. These objectives, such as reducing downtime by a specific percentage or achieving a target OEE, guide implementation efforts and enable progress tracking.
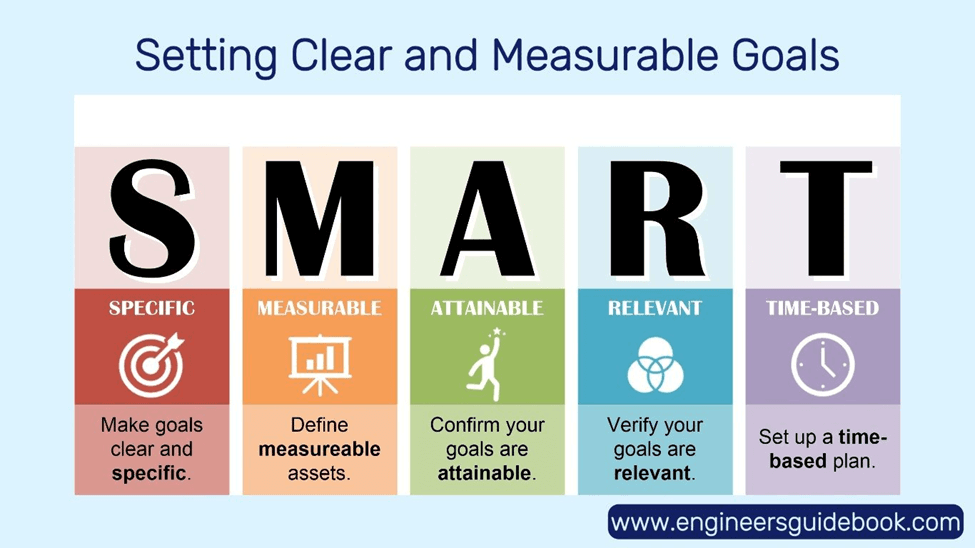
4.4 Developing a Comprehensive Action Plan
An action plan outlines the steps, timelines, and resources required for TPM implementation. This includes prioritizing initiatives, assigning responsibilities, and establishing mechanisms for monitoring and feedback.
5. Tools and Techniques in TPM
5.1 The Role of OEE (Overall Equipment Effectiveness)
OEE serves as a key performance indicator in TPM, measuring the effectiveness of equipment across availability, performance, and quality dimensions. It provides actionable insights for optimizing operations and achieving TPM objectives.
5.2 Root Cause Analysis: Digging Deeper Into Problems
Root cause analysis is a systematic approach to identifying and addressing the underlying causes of equipment failures. By resolving root issues rather than symptoms, organizations can achieve sustainable improvements in reliability.
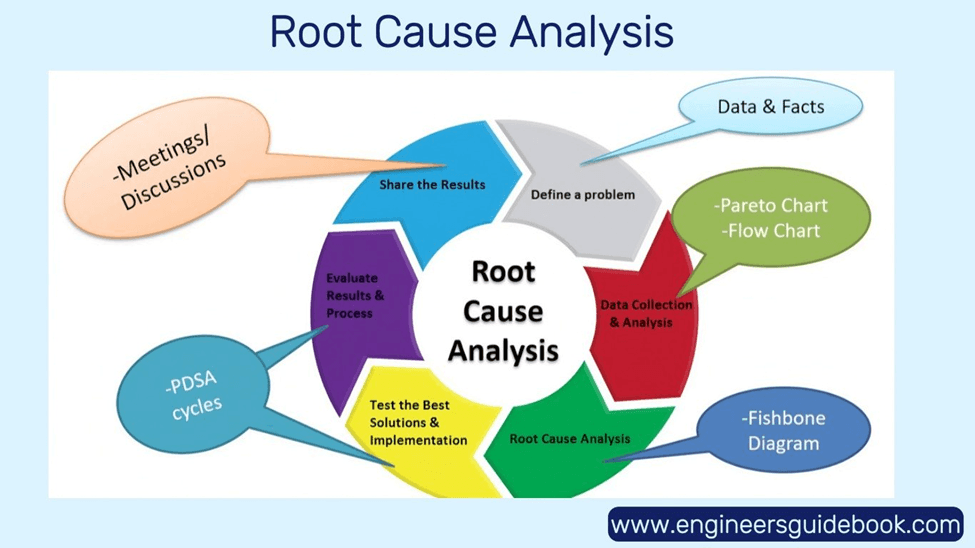
5.3 Visual Management Tools: Aiding Clarity and Communication
Visual management tools, such as charts, dashboards, and color-coded indicators, enhance clarity and communication within the workplace. These tools facilitate real-time monitoring and enable swift decision-making.
5.4 Standard Operating Procedures (SOPs): The Foundation of Consistency
SOPs provide a structured framework for performing maintenance tasks consistently and effectively. By standardizing procedures, organizations can ensure quality, reduce variability, and enhance operational efficiency.
6. Benefits of TPM
6.1 Enhanced Equipment Reliability and Longevity
TPM significantly enhances equipment reliability by addressing maintenance proactively. This extends the lifespan of machinery and reduces the frequency of costly repairs or replacements.
6.2 Improved Production Efficiency and Output
By minimizing downtime and optimizing equipment performance, TPM drives substantial improvements in production efficiency and output. This contributes to higher profitability and customer satisfaction.
6.3 Cost Reduction Through Minimized Downtime
Reducing unplanned downtime translates to significant cost savings. TPM enables organizations to allocate resources more effectively and reduce expenses associated with emergency repairs and lost production time.
6.4 Boosted Morale and Employee Engagement
TPM fosters a culture of ownership and accountability, boosting employee morale and engagement. When employees feel empowered and valued, they are more likely to contribute positively to organizational goals.
7. Overcoming Common Challenges in TPM
7.1 Resistance to Change: Winning Over the Workforce
Resistance to change is a common barrier to TPM implementation. Addressing this requires effective communication, employee involvement, and demonstrating the tangible benefits of TPM initiatives.
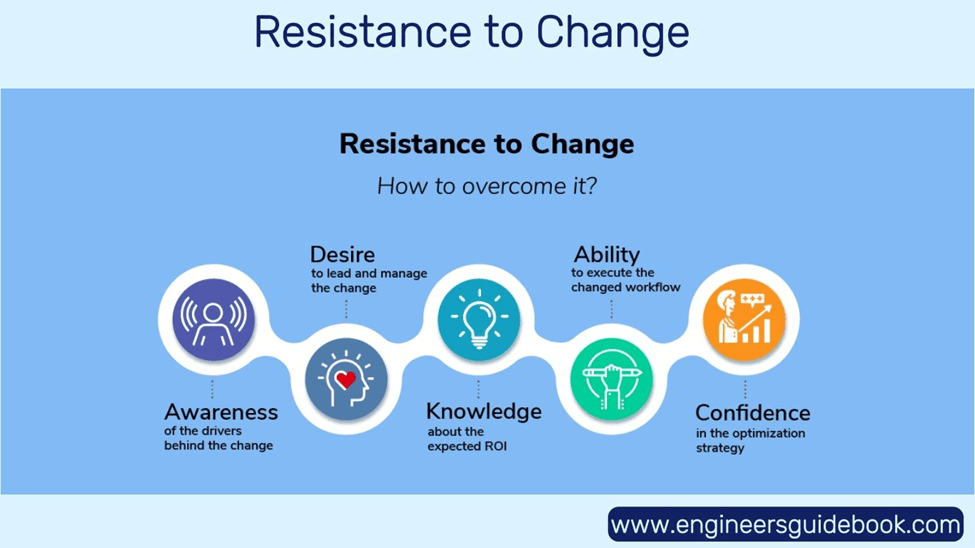
7.2 Aligning TPM With Business Objectives
Aligning TPM with broader business objectives ensures its relevance and sustainability. This involves integrating TPM goals with strategic priorities and demonstrating its impact on organizational performance.
7.3 Sustaining Momentum in the Long Term
Sustaining TPM momentum requires continuous monitoring, regular updates, and ongoing employee engagement. Celebrating successes and reinforcing commitment to TPM principles are key to long-term success.
8. TPM in Different Industries
8.1 TPM in Manufacturing: Case Studies and Success Stories
Manufacturing industries have reaped substantial benefits from TPM, as evidenced by numerous case studies. These success stories highlight the transformative impact of TPM on productivity, quality, and safety.
8.2 Applications of TPM in Food and Beverage Production
In the food and beverage sector, TPM ensures compliance with strict quality and safety standards. By minimizing equipment failures, organizations can maintain consistent product quality and meet regulatory requirements.
8.3 How the Automotive Industry Benefits From TPM
The automotive industry has embraced TPM to enhance efficiency, reduce defects, and meet demanding production schedules. TPM’s emphasis on reliability aligns with the industry’s focus on precision and performance.
8.4 Implementing TPM in Paper Mills and Similar Sectors
In paper mills, where equipment reliability is critical, TPM has proven instrumental in reducing downtime and improving operational efficiency. Similar benefits can be observed in other process-intensive industries.
9. Future Trends in TPM
9.1 The Impact of Industry 4.0 and IoT on TPM
The integration of Industry 4.0 and IoT technologies is revolutionizing TPM. Real-time data monitoring, predictive analytics, and smart sensors are enabling more accurate maintenance strategies and enhancing equipment reliability.
9.2 Predictive Maintenance: The New Frontier
Predictive maintenance leverages data-driven insights to anticipate and address potential failures before they occur. This approach minimizes downtime and optimizes maintenance schedules, paving the way for greater efficiency.
9.3 Sustainable Maintenance Practices
Sustainable maintenance practices focus on reducing environmental impact and promoting resource efficiency. By aligning TPM with sustainability goals, organizations can contribute to a greener future while enhancing operational performance.
10. Case Studies and Real-World Examples
10.1 How a Multinational Corporation Revamped Its Maintenance Strategy
A leading multinational corporation successfully revamped its maintenance strategy by implementing TPM. This case study highlights the challenges faced, solutions implemented, and measurable outcomes achieved.
10.2 Lessons From Small-Scale Industries Implementing TPM
Small-scale industries have also benefited from TPM, demonstrating its adaptability and scalability. These examples underscore the importance of tailored approaches and the potential for significant gains, even with limited resources.
11. Steps to Start TPM in Your Organization
11.1 Getting Leadership Buy-In for TPM
Securing leadership buy-in is crucial for TPM implementation. This involves presenting a compelling business case, highlighting potential benefits, and aligning TPM initiatives with organizational priorities.
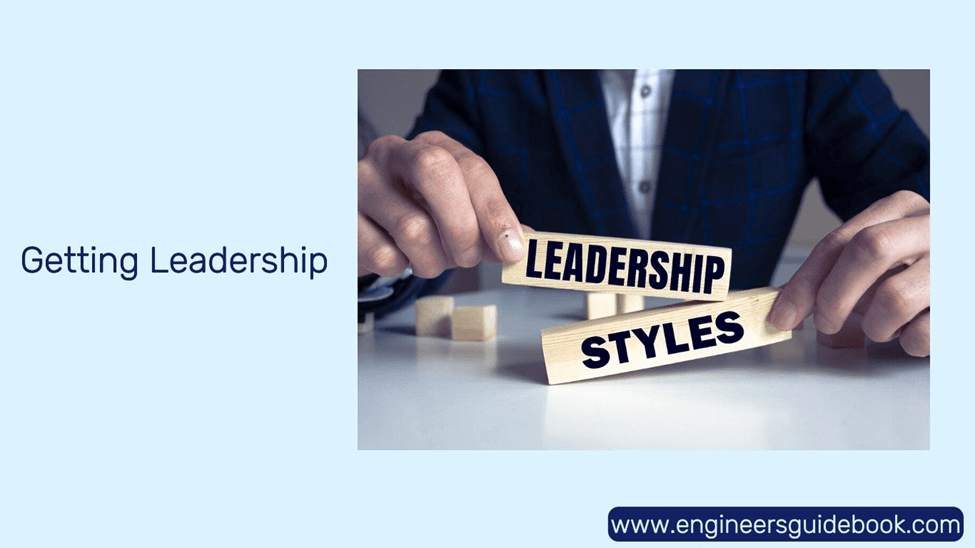
11.2 Pilot Projects: Testing the Waters before Full-Scale Implementation
Pilot projects provide an opportunity to test TPM principles on a smaller scale, identify potential challenges, and refine strategies before full-scale implementation. These initiatives build confidence and generate momentum for broader adoption.
11.3 Monitoring Progress and Refining Strategies
Continuous monitoring and refinement are essential for TPM success. Regular reviews, feedback mechanisms, and data-driven adjustments ensure that TPM initiatives remain effective and aligned with evolving organizational needs.
12. The Role of Leadership in TPM Success
12.1 Inspiring a Culture of Maintenance Excellence
Leadership plays a pivotal role in inspiring a culture of maintenance excellence. By setting the tone, providing resources, and recognizing achievements, leaders can drive organizational commitment to TPM principles.
12.2 How Leaders Can Foster Collaboration across Teams
Collaboration is critical for TPM success. Leaders can foster cross-functional teamwork by breaking down silos, encouraging knowledge sharing, and promoting a unified approach to maintenance and improvement initiatives.
13. Conclusion
TPM delivers long-term value by enhancing efficiency, reducing costs, and fostering a culture of continuous improvement. In a competitive landscape, these advantages provide a significant edge.
Embarking on the TPM journey requires vision, commitment, and a willingness to embrace change. Organizations that invest in TPM stand to reap substantial benefits, paving the way for sustained success and growth.
14. FAQS
1. What is Total Productive Maintenance (TPM)?
TPM is a holistic approach to equipment maintenance aimed at maximizing efficiency by preventing breakdowns, defects, and accidents. It integrates maintenance into daily operations and empowers employees at all levels to take ownership of maintenance tasks.
2. What are the main goals of TPM?
The primary goals of TPM are achieving zero breakdowns, zero defects, and zero accidents. These objectives enhance productivity, ensure product quality, and create a safer workplace.
3. What are the eight pillars of TPM?
The eight pillars of TPM are:
- Autonomous Maintenance
- Planned Maintenance
- Quality Maintenance
- Focused Improvement
- Early Equipment Management
- Training and Education
- Safety, Health, and Environment
- Office TPM
4. How does TPM differ from traditional maintenance?
Traditional maintenance is often reactive, addressing issues after they occur. TPM, on the other hand, focuses on proactive and preventive measures, integrating maintenance into everyday operations and involving all employees.
5. What is Overall Equipment Effectiveness (OEE), and why is it important in TPM?
OEE measures equipment efficiency by analyzing availability, performance, and quality. It is a key metric in TPM for identifying areas of improvement and optimizing operational performance.
6. How can organizations implement TPM effectively?
Effective TPM implementation involves assessing current maintenance strategies, setting measurable goals, forming a steering committee, conducting pilot projects, and providing employee training. Continuous monitoring and refinement are essential for long-term success.
7. What industries benefit most from TPM?
While TPM is widely used in manufacturing, it is also beneficial in industries like food and beverage production, automotive, paper mills, and other process-intensive sectors where equipment reliability and efficiency are critical.
8. How does TPM align with Industry 4.0 technologies?
TPM integrates seamlessly with Industry 4.0 technologies like IoT and predictive analytics. These tools enable real-time monitoring, data-driven decision-making, and predictive maintenance, enhancing the overall effectiveness of TPM strategies.
2 Responses
I love your blog.. very nice colors & theme. Did you create this website yourself or did you
hire someone to do it for you? Plz answer back as I’m looking to design my own blog
and would like to know where u got this from. many thanks
i wonder how you can get such informationa and did you write this all by you information?