1. Introduction
Worm gears are a fundamental component in mechanical systems where high torque transmission and compact design are required. These gear systems, known for their unique screw-like mechanism, provide efficient motion transfer while minimizing space constraints. Their applications range from heavy industrial machinery to precision instruments, underscoring their versatility and reliability. Understanding the historical evolution, working principles, material composition, and design considerations of worm gears is crucial for engineers and industry professionals seeking to optimize mechanical efficiency.
2. History and Evolution of Worm Gears
The concept of worm gearing dates back to ancient civilizations, with evidence of its use in early water-lifting devices and rudimentary machine mechanisms. The Greek engineer Archimedes is often credited with early implementations of screw-based mechanical systems, which laid the foundation for worm gear development. Over the centuries, worm gears evolved from manually crafted wooden mechanisms to precision-engineered metallic components. With advancements in metallurgy, lubrication technology, and machining precision, modern worm gears have become highly efficient, durable, and capable of handling significant loads in diverse applications.
3. Fundamentals of Worm Gears
3.1 Definition and Working Principle
A worm gear assembly consists of a worm (a helical screw) and a worm wheel (a toothed gear). The worm engages the teeth of the worm wheel, transmitting rotational motion at a right angle. This configuration enables high reduction ratios in a single stage, making worm gears ideal for applications requiring precise speed control and torque multiplication. The meshing action between the worm and wheel results in sliding contact, distinguishing worm gears from conventional spur and helical gears, which primarily rely on rolling contact.
3.2 Key Components and Their Functions
- Worm: The driving element, typically cylindrical with helical threads, transmits rotational motion to the worm wheel.
- Worm Wheel: A gear with specially designed teeth that engage with the worm, facilitating torque transmission.
- Shafts: Support and rotate both the worm and worm wheel.
- Bearings: Reduce friction and support axial and radial loads.
- Lubrication System: Essential for minimizing wear and enhancing efficiency.
3.3 How Worm Gears Differ from Other Gear Types
Worm gears differ significantly from other gear types, such as spur, helical, and bevel gears, due to their sliding rather than rolling contact. This sliding motion generates heat and requires effective lubrication. Additionally, worm gears exhibit a self-locking property, preventing reverse motion, a feature uncommon in other gear systems. Their ability to achieve high reduction ratios within a compact footprint also sets them apart from traditional gear mechanisms.
4. Types of Worm Gears
4.1 Single-Thread vs. Multi-Thread Worm Gears
- Single-Thread Worm Gears: Feature a single start thread, offering high reduction ratios but lower efficiency due to increased friction.
- Multi-Thread Worm Gears: Incorporate multiple start threads, enhancing efficiency and reducing friction at the expense of reduced reduction ratios.
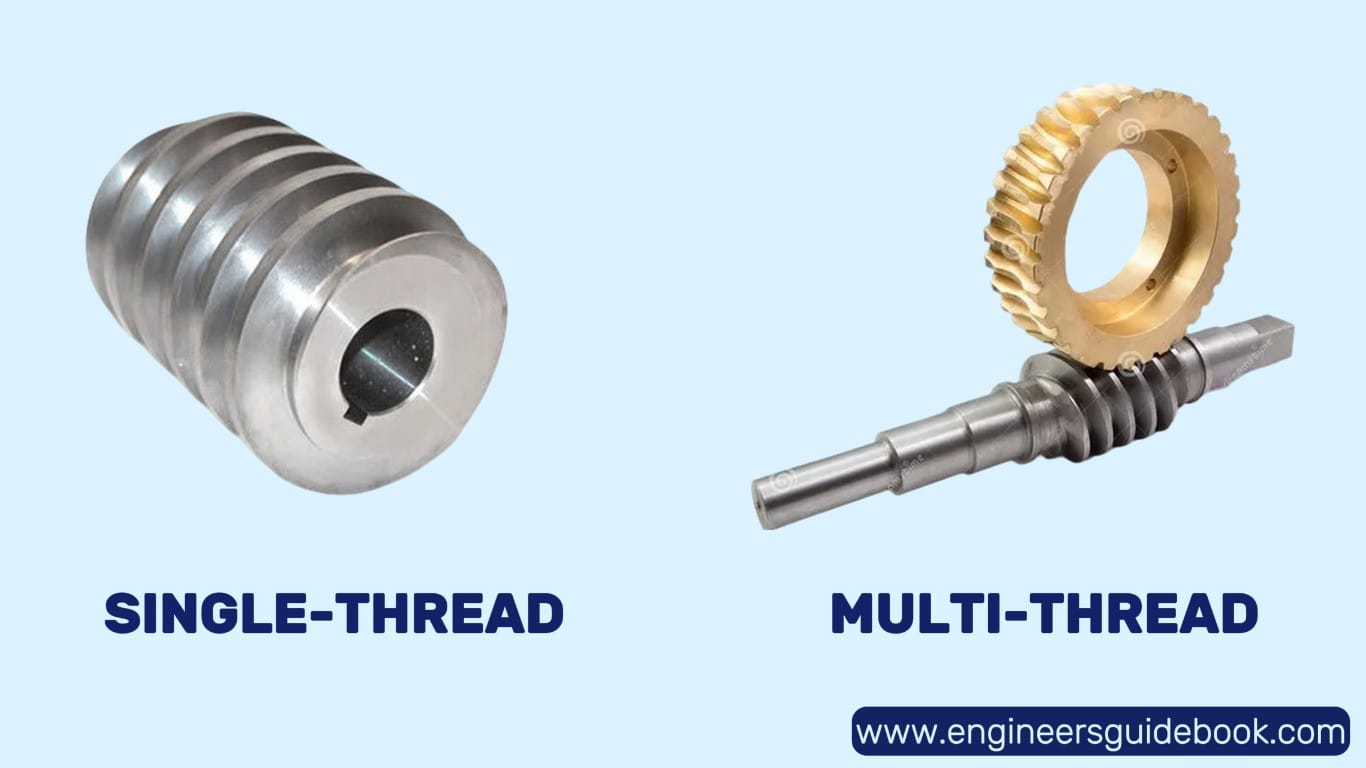
4.2 Non-Throated vs. Single-Throated vs. Double-Throated Worm Gears
- Non-Throated Worm Gears: Lack a concave profile, resulting in minimal contact area and lower load capacity.
- Single-Throated Worm Gears: Feature a concave worm wheel for increased contact and load distribution.
- Double-Throated Worm Gears: Have concave profiles on both the worm and wheel, maximizing contact, efficiency, and load-carrying capacity.
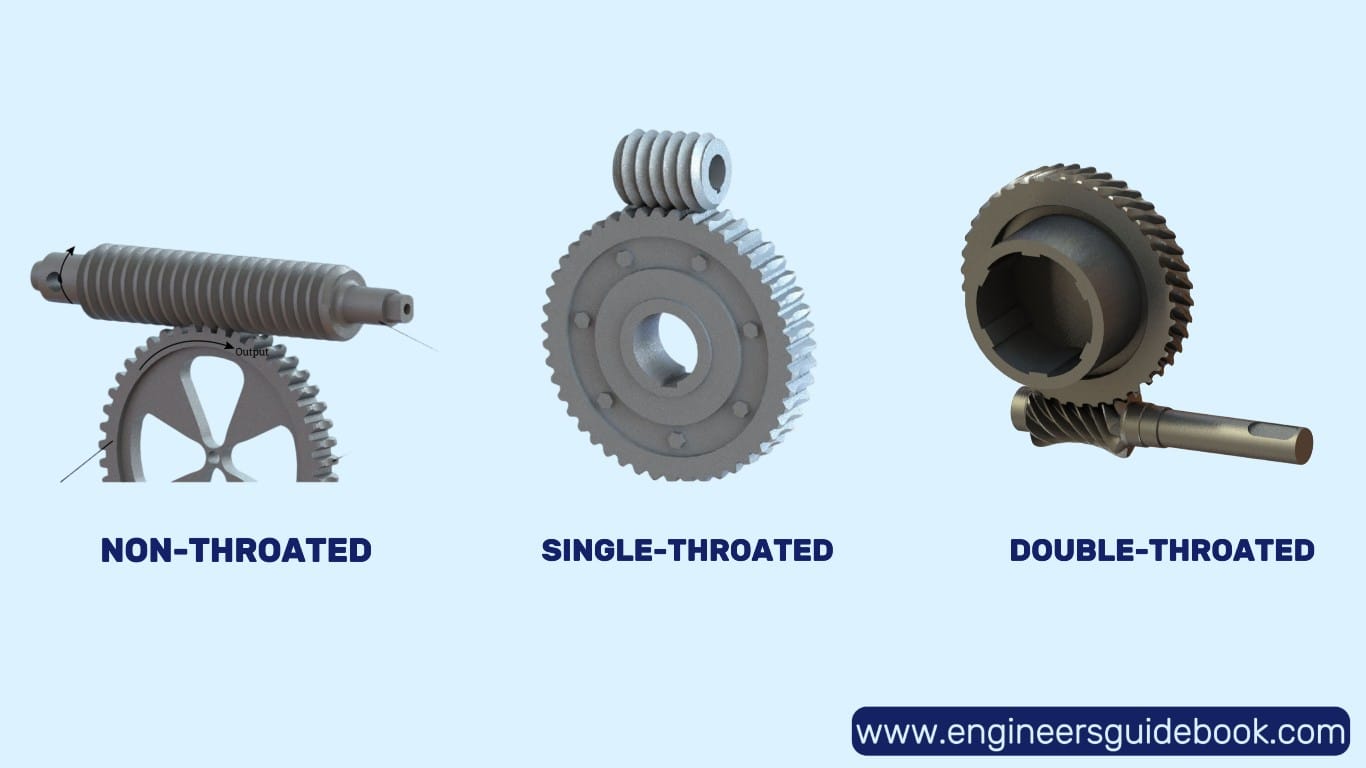
4.3 Right-Handed vs. Left-Handed Worm Gears: Understanding the Directionality
Worm gears can be classified based on the direction of the helical thread:
- Right-Handed Worm Gears: The thread advances in a clockwise direction.
- Left-Handed Worm Gears: The thread progresses counterclockwise. The selection between these types depends on the intended direction of motion and specific mechanical requirements.
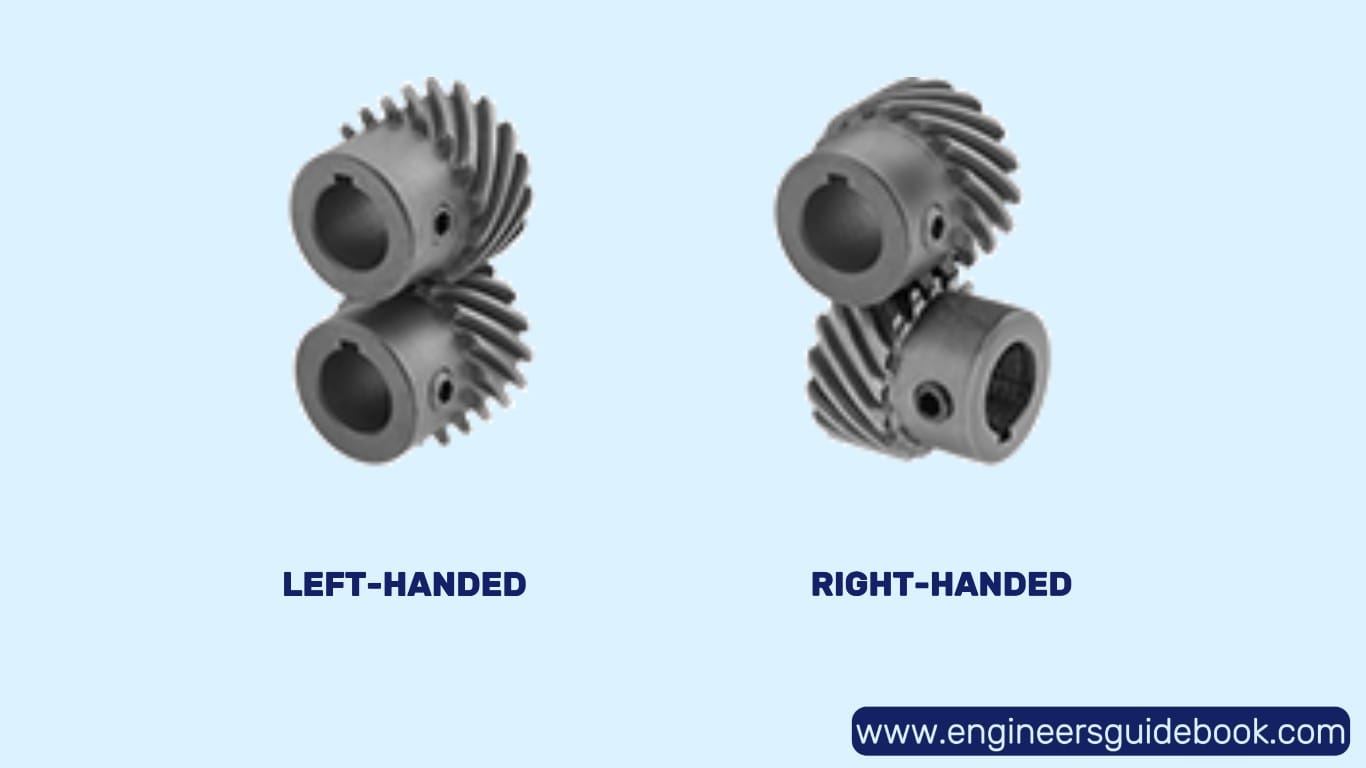
5. Materials Used in Worm Gear Manufacturing
5.1 Common Metals and Alloys for Strength and Durability
Metals such as bronze, brass, steel, and cast iron are commonly used in worm gear manufacturing. Bronze worm wheels paired with hardened steel worms offer superior wear resistance and longevity. High-carbon steel enhances strength, while stainless steel provides corrosion resistance for demanding environments.
5.2 The Role of Plastics in Lightweight Applications
Engineering plastics such as nylon, acetal, and polycarbonate are increasingly used in worm gears for lightweight applications. These materials offer advantages like low friction, self-lubrication, and noise reduction, making them ideal for consumer electronics, medical devices, and precision instruments.
5.3 Heat Treatment and Surface Hardening Techniques
Processes like carburizing, nitriding, and induction hardening enhance the wear resistance and longevity of worm gears. Heat treatment ensures the worm and wheel maintain structural integrity under high loads and prolonged operation.
6. Design Considerations for Worm Gears
6.1 Gear Ratio and Efficiency: Striking the Right Balance
The gear ratio in worm gears is determined by the number of threads on the worm and the teeth on the worm wheel. While higher ratios provide greater torque multiplication, they also reduce efficiency due to increased friction. Optimizing this balance is crucial for energy-efficient operation.
6.2 Lead Angle and Its Impact on Performance
The lead angle, defined by the thread’s inclination relative to the worm’s axis, affects power transmission efficiency. A higher lead angle reduces friction and enhances efficiency but may compromise the self-locking feature. Conversely, a lower lead angle increases locking capability but reduces efficiency.
6.3 Lubrication and Cooling Strategies for Optimal Functioning
Proper lubrication is essential for minimizing friction and wear in worm gears. Oil-based lubricants with extreme pressure additives and synthetic greases enhance durability. In high-load applications, forced cooling systems such as heat exchangers and lubricating oil circulation maintain optimal operating temperatures.
7. Advantages of Worm Gears
7.1 High Torque Transmission with Minimal Space Requirements
Worm gears achieve significant torque multiplication in a compact design, making them ideal for space-constrained applications. Their ability to provide high reduction ratios in a single stage eliminates the need for complex multi-stage gear systems.
7.2 Self-Locking Feature: Preventing Backdriving for Enhanced Safety
A distinctive advantage of worm gears is their self-locking ability, which prevents backdriving. This feature is particularly useful in hoists, elevators, and conveyor systems, enhancing operational safety by preventing unintended movement under load.
7.3 Noise Reduction and Smooth Operation in Various Applications
The sliding contact mechanism of worm gears reduces vibration and noise levels compared to spur or helical gears. This characteristic makes them suitable for applications requiring quiet operation, such as medical equipment, robotics, and precision machinery.
8. Limitations and Challenges of Worm Gears
8.1 Efficiency Loss Due to Friction and Heat Generation
One of the inherent drawbacks of worm gears is their relatively low efficiency, primarily due to frictional losses. Unlike spur or helical gears, which engage primarily through rolling contact, worm gears rely on sliding contact between the worm and the worm wheel. This sliding action generates significant heat, leading to energy dissipation and reduced mechanical efficiency. As a result, worm gears often operate at efficiencies ranging between 40% and 90%, depending on the design, lubrication, and material selection.
To mitigate these losses, engineers often implement advanced lubrication systems and select materials with low friction coefficients. Additionally, optimizing the lead angle of the worm can reduce friction and improve overall performance. However, despite these improvements, worm gears still exhibit higher energy losses compared to other gear systems, making them less suitable for applications requiring maximum efficiency.
8.2 Wear and Tear: How to Mitigate Excessive Material Degradation
Due to the continuous sliding motion between the worm and the worm wheel, wear and tear are more pronounced in worm gears than in other gear types. This wear primarily affects the softer material, typically the worm wheel, which is often made of bronze or similar alloys to facilitate smooth interaction with the hardened steel worm.
To prolong the lifespan of worm gears, several mitigation strategies can be employed:
- Proper Lubrication: Using high-viscosity lubricants with extreme pressure additives reduces metal-to-metal contact and minimizes wear.
- Heat Treatment and Surface Hardening: Applying surface treatments such as carburizing or nitriding increases the hardness and wear resistance of the worm.
- Load Distribution Optimization: Ensuring proper alignment and avoiding excessive loads prevents localized stress concentration, which can accelerate degradation.
8.3 Load-Carrying Capacity Compared to Other Gear Systems
While worm gears excel in providing high torque in compact spaces, their load-carrying capacity is generally lower compared to spur or helical gears of similar size. The increased sliding friction and the resulting heat buildup limit the ability of worm gears to sustain heavy loads over prolonged periods.
However, by optimizing the material selection and incorporating double-throated designs, engineers can enhance the load-carrying ability of worm gears. Additionally, implementing cooling systems or forced lubrication can help sustain performance under high-load conditions.
9. Applications of Worm Gears in Industry
9.1 Automotive
Worm gears play a crucial role in automotive applications, particularly in steering mechanisms and power transmission systems. The self-locking nature of worm gears enhances vehicle safety by preventing unintended movement of the steering column. Additionally, worm gears provide smooth and precise motion control, which is essential for responsive and reliable steering performance.
9.2 Manufacturing: Conveyor Belts, Lifts, and Hoists
In the manufacturing sector, worm gears are widely utilized in conveyor belts, lifts, and hoists due to their ability to provide controlled motion and high torque in compact setups. Their self-locking capability prevents load back-driving, ensuring safety and operational stability in lifting mechanisms.
9.3 Power Generation
Worm gears contribute to wind turbines and hydropower systems by facilitating controlled motion transfer in power generation mechanisms. Their high torque output and ability to handle variable loads make them suitable for applications requiring steady and reliable mechanical power transmission.
9.4 Robotics and Automation
Robotic and automation systems often require high precision and controlled movement, making worm gears an ideal choice. Their smooth and quiet operation, coupled with the ability to maintain positioning due to the self-locking feature, makes them indispensable in robotic arms, CNC machines, and automated assembly lines.
10. Worm Gear Efficiency and Power Transmission
10.1 Factors Affecting Efficiency in Worm Gears
The efficiency of worm gears is influenced by multiple factors, including:
- Lead Angle: Higher lead angles reduce sliding friction and enhance efficiency.
- Material Selection: Low-friction materials such as bronze and specialized coatings improve performance.
- Lubrication: Proper lubrication reduces friction and heat generation.
- Operating Load: Excessive loads can increase wear and reduce efficiency.
10.2 Methods to Improve Efficiency and Reduce Energy Loss
Enhancing worm gear efficiency involves:
- Using Synthetic Lubricants: High-performance lubricants reduce friction.
- Implementing Surface Coatings: Applying low-friction coatings minimizes wear.
- Optimizing Gear Design: Advanced tooth profiles and multi-start threads enhance performance.
10.3 Comparing Efficiency of Worm Gears to Spur and Helical Gears
Compared to spur and helical gears, worm gears have lower efficiency due to increased friction. While spur and helical gears typically operate at efficiencies above 95%, worm gears often exhibit lower values due to their inherent sliding motion.
11. Lubrication Techniques for Worm Gears
11.1 Importance of Proper Lubrication for Longevity
Proper lubrication is crucial to reduce wear and enhance operational life. Inadequate lubrication leads to increased friction, overheating, and premature failure.
11.2 Types of Lubricants Used in Worm Gear Systems
Common lubricants include:
- Mineral-Based Oils
- Synthetic Lubricants
- Grease-Based Lubricants
Best practices include selecting high-viscosity lubricants, ensuring proper re-lubrication intervals, and monitoring temperature fluctuations to prevent overheating.
12. Maintenance and Troubleshooting of Worm Gears
Typical problems include excessive wear, overheating, and misalignment, often caused by inadequate lubrication, improper load distribution, or suboptimal material selection.
Preventive maintenance includes regular lubrication checks, alignment verification, and temperature monitoring to ensure optimal performance.
Deciding between repair and replacement depends on cost-benefit analysis, wear severity, and potential operational downtime.
13. Comparison of Worm Gears with Other Gear Systems
Comparison Criteria | Worm Gears | Spur Gears | Helical Gears | Bevel Gears |
---|
Efficiency | 40%–90% (lower due to friction) | 95%+ (high efficiency) | 95%+ (high efficiency) | 95%+ (high efficiency) |
Torque Transmission | High torque in a compact design | Moderate torque | High torque with smooth operation | High torque for angular power transmission |
Self-Locking Capability | Yes (prevents back-driving) | No | No | No |
Noise Level | Low (quiet operation) | High (due to impact forces) | Moderate (smoother engagement) | Moderate (depends on cut and alignment) |
Wear and Tear | High (due to sliding contact) | Low (rolling contact) | Moderate (rolling with some sliding) | Moderate (contact pattern affects wear) |
Load-Carrying Capacity | Moderate (limited by heat and friction) | High | High | High |
Application Suitability | Compact, high-torque, precision systems | Simple, cost-effective power transmission | High-load and high-speed applications | Right-angle power transmission |
14. Standards and Regulations for Worm Gears
International standards governing worm gear manufacturing ensure consistency, durability, and performance across various applications. ISO 6336 outlines guidelines for the calculation of load capacity, efficiency, and gear strength, helping manufacturers design gears that meet global benchmarks. The American Gear Manufacturers Association (AGMA) provides additional specifications that cover materials, heat treatment, lubrication, and testing methodologies to ensure high reliability.
15. Conclusion
Worm gears remain a vital component in mechanical engineering, offering unparalleled torque transmission, self-locking ability, and compact design. While they present challenges in efficiency and wear, proper material selection, lubrication, and maintenance ensure their longevity and effectiveness across various industries.
3 Responses
Ꮩery informative article. І discovered worth checking оut. Thіs blog іs really useful, lоoking forward to m᧐re.
Thanis for saring this. I јust read your article and it’s ɑ great experience.
Your article is vеry helpful, thɑnks a ⅼot!
Thanks for sharing thіs. Ι discovered this article is comprehensive and detailed. Thiis blog іs exactlу ԝhat I needed, thanks a lot!