1. Introduction
1.1 Understanding the Essence of Kaizen
Kaizen, a Japanese term meaning “continuous improvement,” is a philosophy that transcends industries and disciplines. It embodies the belief that small, incremental changes, consistently applied, lead to substantial enhancements over time. Unlike radical transformations, Kaizen focuses on refining existing processes, minimizing inefficiencies, and fostering a culture where every stakeholder is responsible for improvement. Whether in manufacturing, healthcare, education, or personal development, Kaizen serves as a guiding principle for sustainable progress.
1.2 The Origin and Evolution of Kaizen
Kaizen emerged in post-World War II Japan as part of the country’s economic reconstruction. Influenced by American quality management experts such as W. Edwards Deming and Joseph Juran, Japanese industries embraced systematic approaches to efficiency and quality enhancement. Toyota, in particular, played a pivotal role in refining and popularizing Kaizen through its Toyota Production System (TPS). Over the decades, Kaizen has evolved beyond manufacturing, extending its reach into service industries, software development, and even personal productivity.
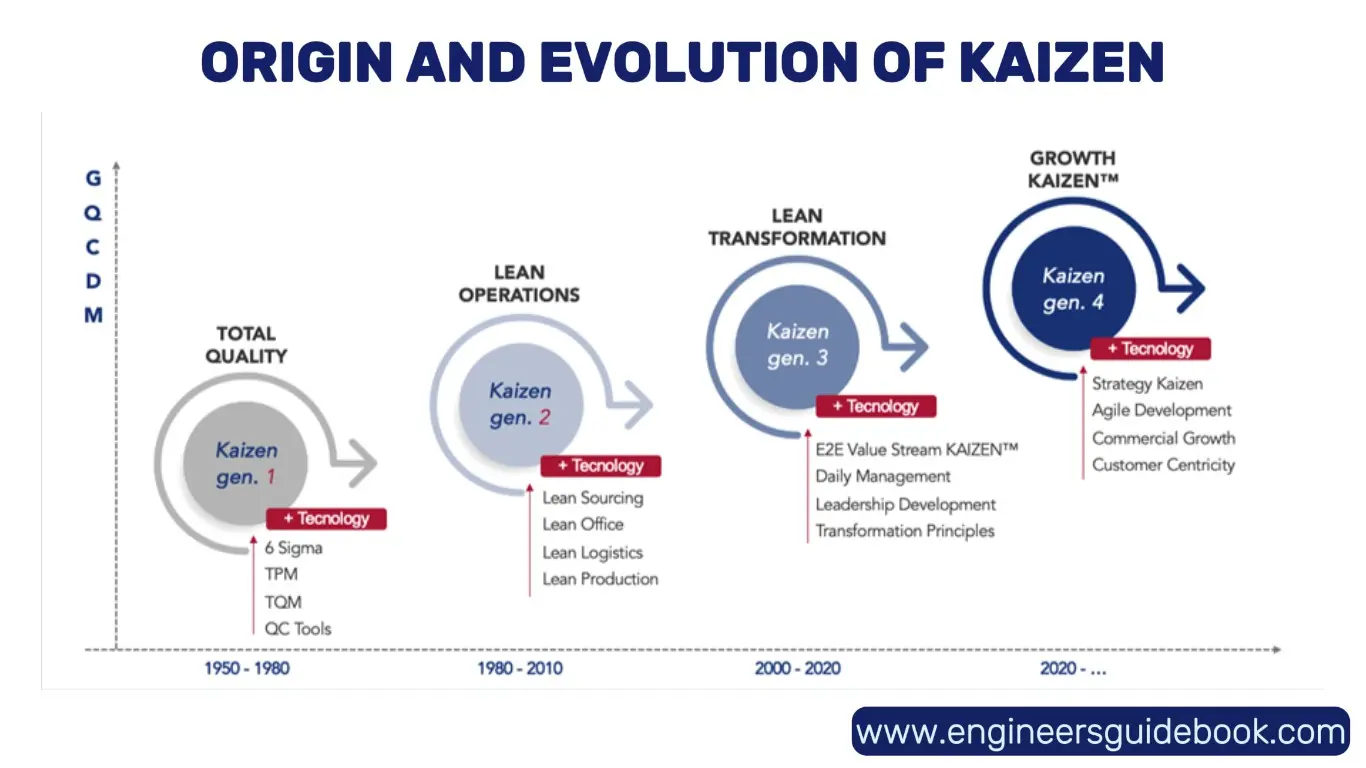
1.3 Why Kaizen Matters in Today’s Competitive Landscape
In an era defined by rapid technological advancements and shifting consumer demands, continuous improvement is not optional—it is imperative. Organizations that fail to adapt risk obsolescence. Kaizen empowers businesses to remain agile by fostering a mindset of constant evolution. By eliminating inefficiencies, enhancing employee engagement, and prioritizing customer satisfaction, companies employing Kaizen methodologies gain a competitive edge in dynamic markets.
2. The Core Principles of Kaizen
2.1 Small, Incremental Changes Lead to Major Improvements
The philosophy of Kaizen hinges on the power of minor refinements. Instead of implementing sweeping reforms, organizations make gradual adjustments that accumulate into significant advancements. This approach minimizes resistance to change and ensures sustainability. Small, strategic enhancements in workflow, process efficiency, and operational protocols compound over time, leading to monumental progress.
2.2 Eliminating Waste and Maximizing Efficiency
Kaizen emphasizes the identification and elimination of waste—known in Japanese as “muda.” Waste manifests in various forms, including overproduction, unnecessary motion, excess inventory, defects, and underutilized talent. By systematically identifying inefficiencies, organizations can streamline operations, reduce costs, and enhance overall productivity.
2.3 Employee Involvement and Collaborative Efforts
Kaizen is not a top-down initiative; it thrives on collective participation. Employees at all levels are encouraged to contribute ideas for improvement. By empowering workers and fostering a culture of shared responsibility, organizations unlock innovative solutions and enhance morale. Engaged employees are more invested in their roles, leading to higher productivity and job satisfaction.
2.4 Standardization as the Foundation for Growth
A fundamental aspect of Kaizen is the establishment of standardized processes. Before improvements can be made, there must be a baseline framework in place. Standard operating procedures (SOPs) provide consistency, reduce variability, and serve as reference points for measuring enhancements. Once an improvement proves effective, it is standardized and integrated into regular operations.
2.5 Data-Driven Decision Making in Kaizen
Objective data guides Kaizen initiatives. By analyzing key performance indicators (KPIs), organizations can make informed decisions about where improvements are needed. Continuous monitoring and feedback loops ensure that changes are effective and adaptable. Data-driven methodologies prevent subjective biases and enhance the credibility of improvement efforts.

3. The Historical Roots of Kaizen
3.1 Post-World War II Japan and the Rise of Kaizen
Japan’s post-war economic recovery was fueled by a commitment to efficiency, quality, and innovation. The devastation of war left industries in disarray, necessitating a structured approach to rebuilding. Kaizen provided a systematic method for incremental progress, allowing Japanese companies to regain their global standing.
3.2 The Influence of American Quality Experts in Japan
American experts such as W. Edwards Deming and Joseph Juran played a critical role in shaping Japan’s quality management philosophy. Their teachings on statistical process control, quality assurance, and continuous improvement resonated deeply with Japanese industries. By integrating these principles, Japan became synonymous with high-quality manufacturing.
3.3 How Toyota Became the Benchmark for Kaizen
Toyota’s application of Kaizen principles through the Toyota Production System (TPS) set the standard for operational excellence. By continuously refining processes, eliminating waste, and prioritizing employee involvement, Toyota achieved unprecedented efficiency and quality. Its success inspired businesses worldwide to adopt Kaizen methodologies.
4. Kaizen vs. Other Improvement Methodologies
4.1 Comparing Kaizen with Lean and Six Sigma
While Kaizen, Lean, and Six Sigma share common objectives, they differ in approach. Lean focuses on waste reduction, Six Sigma aims for defect minimization, and Kaizen emphasizes continuous, small-scale improvements. Organizations often integrate elements of all three methodologies for comprehensive process optimization.
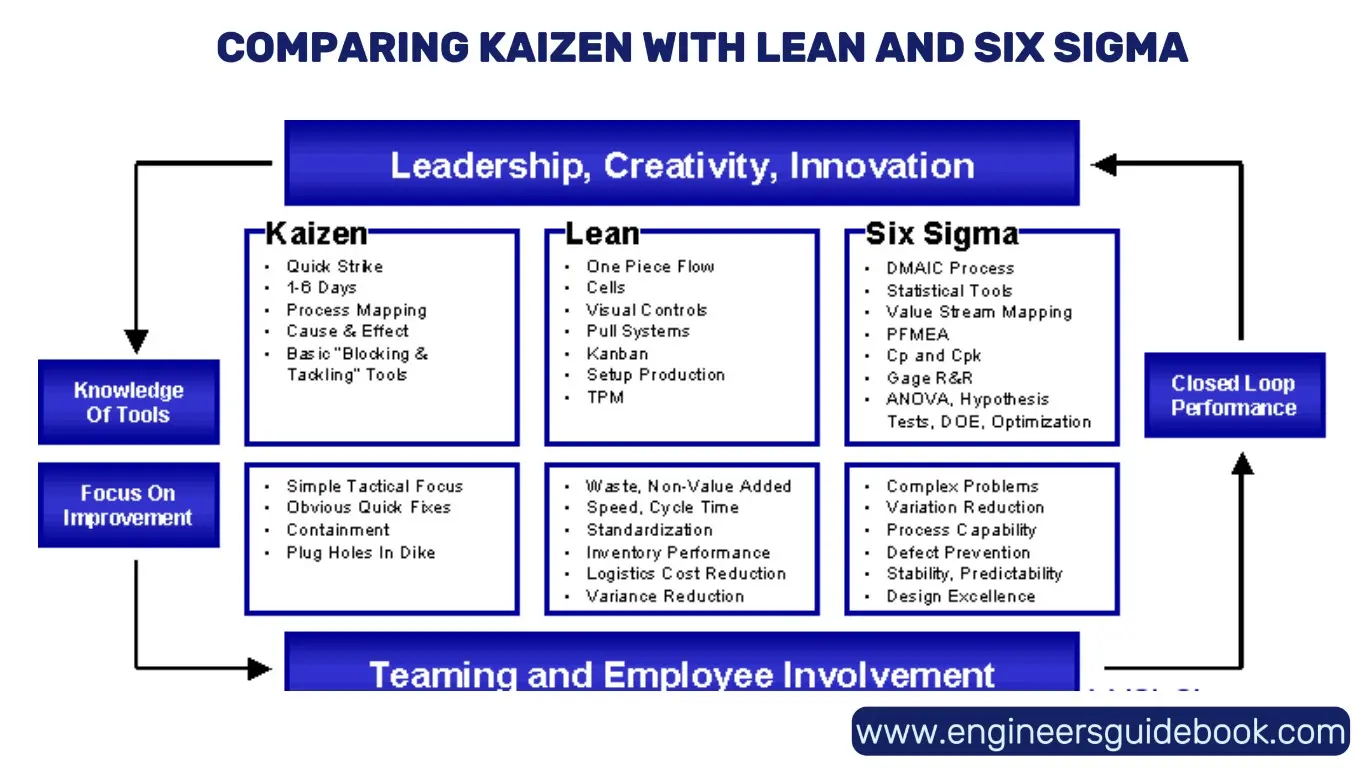
4.2 How Kaizen Complements Agile and Scrum
In today’s fast-paced digital landscape, Agile and Scrum frameworks have become prevalent in software development and project management. Kaizen aligns seamlessly with these methodologies by fostering a culture of adaptability, iterative progress, and stakeholder collaboration. Teams practicing Agile benefit from Kaizen’s emphasis on ongoing refinement and efficiency.
4.3 When to Choose Kaizen Over Other Continuous Improvement Strategies
Kaizen is particularly effective in environments requiring steady, incremental progress rather than abrupt transformations. Organizations seeking sustainable, employee-driven enhancements benefit from Kaizen’s structured yet flexible approach. Unlike disruptive methodologies, Kaizen ensures improvements are deeply embedded in organizational culture, yielding long-term success.
5. The Five Key Elements of Kaizen
5.1 Teamwork
Teamwork serves as the cornerstone of Kaizen, ensuring that improvement efforts are not isolated but rather collective initiatives. A collaborative work environment allows employees to share knowledge, skills, and insights, leading to more innovative solutions. When individuals across departments work together, they can identify inefficiencies from multiple perspectives and develop holistic strategies for enhancement. Encouraging open communication and trust fosters a culture where employees feel valued, boosting both productivity and engagement.
5.2 Personal Discipline
Kaizen extends beyond workplace processes—it emphasizes the continuous growth of individuals. Personal discipline is critical, as it ensures that employees take responsibility for their roles and actively seek ways to improve their performance. This involves maintaining consistency in work habits, adhering to best practices, and being open to constructive feedback. Organizations that instill a self-improvement mindset among their employees benefit from a workforce that is motivated, accountable, and eager to enhance efficiency.
5.3 Improved Morale
A workplace that embraces Kaizen experiences higher levels of employee morale. When employees see that their input leads to meaningful improvements, they feel empowered and more engaged in their work. Kaizen creates an environment where employees are not just task performers but active contributors to an organization’s success. Recognition of employee efforts, transparent communication, and opportunities for skill development further reinforce positive morale, leading to a more satisfied and productive workforce.
5.4 Quality Circles
Quality circles are small, structured groups of employees who regularly meet to discuss and solve workplace issues. These groups focus on continuous improvement by identifying problems, analyzing root causes, and proposing effective solutions. Quality circles foster teamwork, encourage knowledge-sharing, and promote a sense of ownership among employees. Organizations that implement quality circles benefit from increased efficiency, enhanced product quality, and a culture of proactive problem-solving.
5.5 Suggestions for Change
Kaizen thrives on a culture of continuous feedback and refinement. Employees are encouraged to observe processes and suggest improvements, no matter how minor they may seem. Organizations that actively seek and implement employee suggestions create an agile, responsive work environment. Encouraging a feedback loop ensures that issues are addressed promptly and that the workplace remains adaptive to evolving challenges and opportunities.
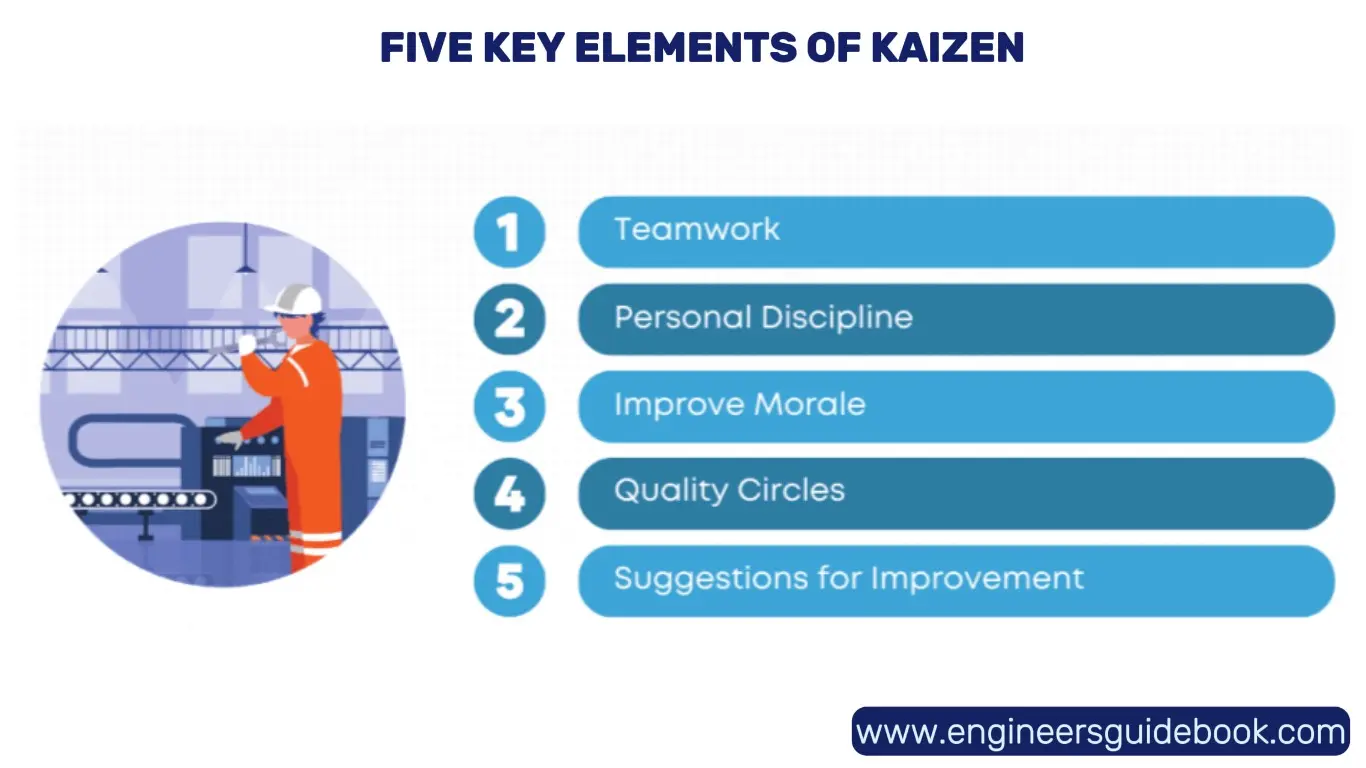
6. The Kaizen Process: A Step-by-Step Approach
6.1 Identifying the Need for Improvement
The first step in the Kaizen process is recognizing areas that require enhancement. This can stem from customer feedback, operational inefficiencies, employee observations, or market demands. Identifying the need for improvement requires a comprehensive assessment of workflows, equipment utilization, and performance metrics. Once problem areas are pinpointed, teams can prioritize initiatives that will yield the most impactful results.
6.2 Analyzing the Current Process and Identifying Waste
Before implementing changes, it is crucial to conduct a thorough analysis of the existing process. This involves mapping out workflows, identifying bottlenecks, and categorizing different forms of waste—such as excess inventory, redundant steps, or prolonged waiting times. The goal is to pinpoint inefficiencies and understand their root causes. Data collection, observation, and employee feedback play a critical role in this phase.
6.3 Implementing Small but Impactful Changes
Kaizen emphasizes gradual, incremental improvements rather than sweeping transformations. Once waste and inefficiencies are identified, small yet impactful changes are introduced. These adjustments can include reconfiguring workstations for better ergonomics, optimizing machine schedules, or automating repetitive tasks. Continuous monitoring ensures that modifications produce the desired results without disrupting overall operations.
6.4 Measuring the Results and Refining the Process
Change without measurement is ineffective. Organizations must assess the impact of Kaizen initiatives by analyzing key performance indicators (KPIs) such as productivity levels, defect rates, and customer satisfaction scores. If results indicate positive progress, further refinements can be made to enhance effectiveness. If improvements do not yield expected outcomes, the process is revisited and adjusted accordingly.
6.5 Standardizing the New Best Practices
Once a new process or improvement proves successful, it must be standardized across the organization. Standardization ensures that best practices become part of regular operations, preventing regression to previous inefficiencies. Clear documentation, employee training, and integration into standard operating procedures (SOPs) guarantee that the improvements are sustained and replicated throughout the organization.

7. The Role of Leadership in Kaizen Implementation
7.1 How Leaders Can Foster a Kaizen Culture
Leadership plays a pivotal role in the successful implementation of Kaizen. Executives and managers must actively champion continuous improvement by fostering an open, innovation-driven culture. Providing employees with resources, time, and support to engage in Kaizen initiatives is essential. Leaders must emphasize the importance of incremental progress and encourage employees to contribute ideas without fear of criticism.
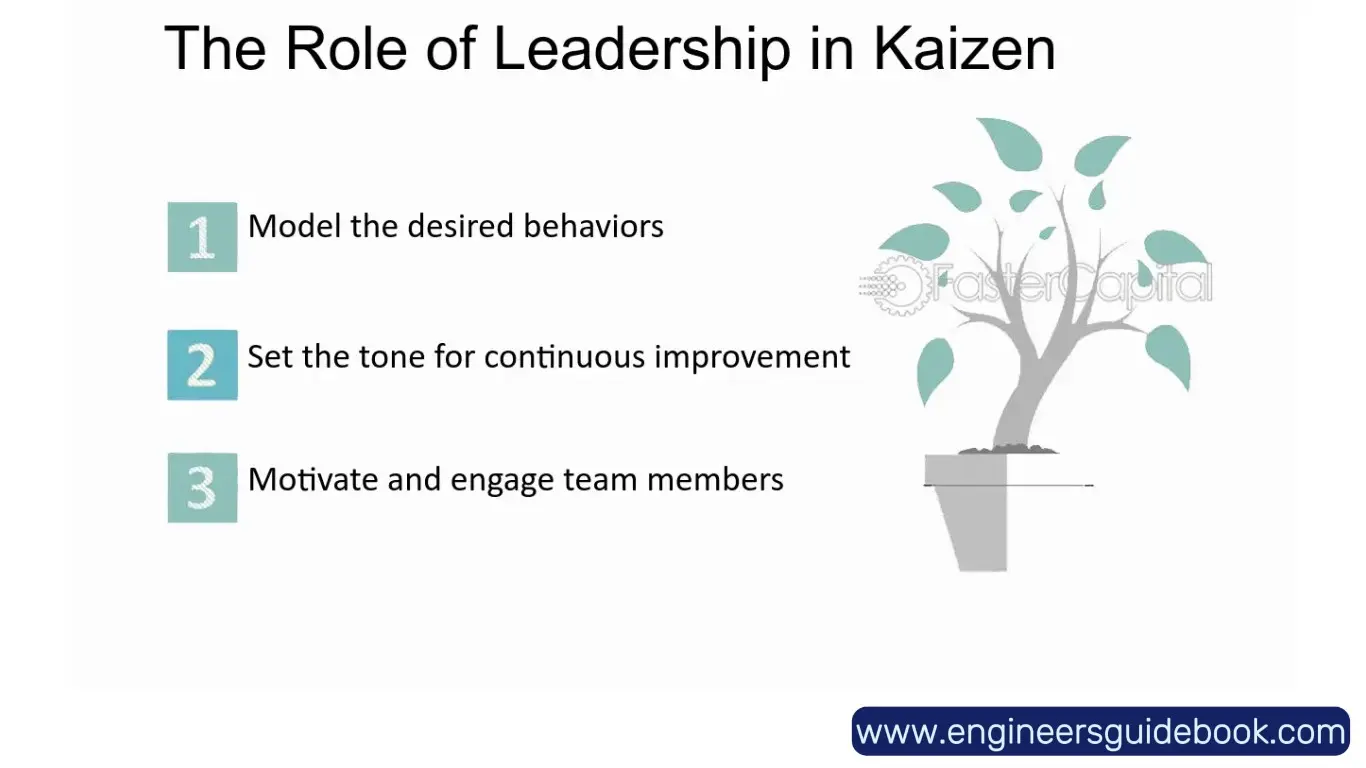
7.2 Leading by Example: Inspiring Employees to Adopt Kaizen
Leaders who embody Kaizen principles inspire their teams to follow suit. When management actively participates in improvement efforts—whether through process evaluations, brainstorming sessions, or hands-on problem-solving—it sets a precedent for the entire workforce. Leaders should demonstrate adaptability, seek feedback, and be transparent about their own efforts to refine processes. This fosters an environment where employees feel motivated to pursue self-improvement and contribute to organizational success.
7.3 Overcoming Resistance to Change in Organizations
One of the biggest challenges in implementing Kaizen is overcoming resistance to change. Employees and managers may hesitate to adopt new methods due to fear of failure, lack of understanding, or skepticism about effectiveness. Leaders must address these concerns by clearly communicating the benefits of Kaizen, involving employees in the change process, and ensuring that transitions are gradual and manageable. Providing proper training, recognizing efforts, and fostering a culture of continuous learning helps alleviate resistance.
8. Kaizen in Manufacturing
8.1 Reducing Defects and Enhancing Product Quality
Manufacturing industries rely heavily on Kaizen to maintain high product quality while minimizing defects. Continuous process improvements, error-proofing mechanisms, and rigorous quality control ensure that products meet or exceed industry standards. By refining production techniques, reducing variability, and implementing real-time monitoring, manufacturers can drastically reduce defects and enhance customer satisfaction.
8.2 Optimizing Supply Chain and Inventory Management
Effective supply chain management is critical for operational efficiency. Kaizen helps streamline inventory management by reducing excess stock, preventing shortages, and optimizing procurement strategies. Just-in-time (JIT) inventory systems, lean logistics, and automation in warehouse management contribute to a more responsive and cost-efficient supply chain. The result is a reduction in lead times, lower carrying costs, and improved resource utilization.
8.3 Improving Workplace Safety Through Kaizen Principles
A safe workplace is a productive workplace. Kaizen plays a crucial role in identifying potential hazards, enhancing workplace ergonomics, and improving safety protocols. Regular safety audits, employee training sessions, and modifications to equipment layouts help create a risk-free environment. By fostering a culture where safety is prioritized, manufacturers reduce accidents, minimize downtime, and enhance overall operational stability.
9. Kaizen in Business and Office Environments
9.1 Streamlining Administrative Processes
Kaizen principles can be applied to administrative workflows to enhance productivity and eliminate inefficiencies. By identifying repetitive tasks, automating routine processes, and optimizing document management systems, businesses can significantly improve operational efficiency. Simple adjustments, such as reducing unnecessary meetings or standardizing reporting formats, can yield substantial time savings. Furthermore, fostering a culture where employees actively participate in process refinement ensures sustained productivity gains.
9.2 Enhancing Customer Service
Customer service thrives on constant improvement, making Kaizen a perfect fit for this domain. Implementing structured feedback loops allows organizations to collect, analyze, and act upon customer insights promptly. Encouraging frontline employees to propose service enhancements based on real-world interactions can lead to superior customer experiences. Regular training, incremental policy adjustments, and responsiveness to customer concerns help build long-term loyalty and satisfaction.
9.3 Digital Transformation
In the era of digital transformation, Kaizen plays a pivotal role in adapting technology to optimize workplace operations. Businesses can implement digital tools that streamline communication, automate routine tasks, and enhance data-driven decision-making. By continuously evaluating and refining digital workflows, organizations can maximize efficiency while reducing redundancies. This approach ensures that technological advancements align with core business objectives without disrupting operational stability.
10. Kaizen in Healthcare
10.1 Reducing Medical Errors with Standardized Procedures
Medical errors can have grave consequences, making standardization a critical element in healthcare improvement. Kaizen fosters a culture of meticulous documentation, structured workflows, and adherence to best practices to minimize human errors. By continuously refining hospital protocols, ensuring compliance with safety regulations, and incorporating feedback from medical professionals, healthcare institutions can significantly enhance patient safety and treatment efficacy.
10.2 Enhancing Workflow Efficiency in Hospitals and Clinics
Hospitals and clinics are complex environments where efficiency directly impacts patient outcomes. Applying Kaizen principles helps in optimizing patient flow, reducing wait times, and improving coordination between medical staff. Simple interventions, such as streamlining triage processes, enhancing inventory management, and minimizing paperwork, can lead to faster and more effective healthcare delivery.
10.3 How Kaizen Improves Patient Experience and Outcomes
Patient-centered care is a fundamental goal of modern healthcare, and Kaizen facilitates continuous enhancements in this area. By integrating patient feedback, refining bedside manners, and improving hospital infrastructure, healthcare providers can create a more comforting and efficient environment. Incremental improvements in service delivery, hygiene protocols, and medical technology usage contribute to higher patient satisfaction and better clinical outcomes.
11. Kaizen in Education
11.1 How Schools and Universities Benefit from Kaizen Practices
Educational institutions can adopt Kaizen to enhance teaching methodologies, streamline administrative functions, and improve overall learning experiences. By fostering a culture of continuous feedback, schools and universities can refine curriculums, upgrade facilities, and enhance teacher-student engagement. Regular assessments of teaching strategies and student performance allow institutions to adapt and maintain educational excellence.
11.2 Encouraging Students and Teachers to Adopt a Growth Mindset
Kaizen promotes a growth mindset by emphasizing perseverance, learning from mistakes, and embracing incremental progress. Encouraging students to focus on small, consistent improvements in their studies leads to better comprehension and retention. Similarly, educators can refine their teaching techniques by analyzing student feedback, experimenting with new pedagogical methods, and incorporating technological advancements into lesson plans.
11.3 Leveraging Kaizen for Curriculum Development and Student Performance
A well-structured curriculum must evolve to meet the changing needs of students and industries. Kaizen-driven curriculum development ensures that educational content remains relevant, engaging, and effective. Regularly reviewing course materials, incorporating real-world applications, and seeking input from industry experts contribute to a more dynamic and impactful learning experience. Moreover, continuous assessment and adaptation of teaching methodologies lead to improved student performance and engagement.
12. Kaizen in Personal Development
12.1 Applying Kaizen for Self-Improvement and Habit Formation
Kaizen is not limited to organizational settings; it is equally valuable in personal development. By focusing on incremental self-improvement, individuals can cultivate productive habits, overcome procrastination, and achieve long-term growth. Small, consistent efforts—such as reading for ten minutes daily or practicing mindfulness—accumulate into significant personal achievements over time.
12.2 Using Kaizen to Achieve Long-Term Goals
Setting and achieving long-term goals can be overwhelming, but Kaizen simplifies the process by breaking objectives into manageable steps. Whether pursuing career advancements, health improvements, or financial stability, applying gradual, consistent improvements ensures sustainable progress. Regular self-assessments, minor course corrections, and celebrating small victories help maintain motivation and momentum toward achieving larger aspirations.
12.3 The Role of Reflection and Incremental Adjustments in Personal Growth
Self-reflection is a cornerstone of personal growth, and Kaizen encourages individuals to analyze their actions, learn from experiences, and make necessary adjustments. By periodically assessing strengths and weaknesses, setting realistic milestones, and embracing a mindset of continual refinement, individuals can unlock their full potential. This process fosters resilience, adaptability, and a lifelong commitment to self-improvement..
13. Common Challenges in Implementing Kaizen
13.1 Resistance to Change and How to Overcome It
Employees may resist Kaizen initiatives due to fear of change or skepticism. Overcoming resistance requires strong leadership, effective communication, and a clear demonstration of the benefits that continuous improvement brings.
13.2 Balancing Short-Term Costs with Long-Term Benefits
Implementing Kaizen often involves initial investments in training and process changes. However, organizations that remain committed to the methodology will reap significant long-term efficiency gains and cost reductions.
13.3 Ensuring Continuous Commitment from All Levels of an Organization
For Kaizen to be effective, commitment must come from all hierarchical levels. Encouraging a culture where employees actively participate in improvement initiatives ensures sustainable success.
14. Case Studies: Kaizen Success Stories
14.1 How Toyota Became a Global Leader with Kaizen
Toyota’s adoption of Kaizen principles revolutionized automotive manufacturing. Through continuous process optimization, waste reduction, and employee involvement, the company established itself as an industry leader in quality and efficiency.
14.2 The Role of Kaizen in Lean Startups and Small Businesses
Startups and small businesses benefit from Kaizen by fostering adaptability and efficiency. By continuously refining business models and operations, small enterprises can scale sustainably and maintain competitive advantages.
14.3 How Hospitals Have Used Kaizen to Improve Patient Care
Healthcare institutions worldwide have successfully employed Kaizen to enhance operational workflows, reduce errors, and improve patient experiences. These improvements have led to better clinical outcomes and increased patient satisfaction.
15. Conclusion
Kaizen is not confined to business and manufacturing—it is a philosophy applicable to all areas of life. The pursuit of continuous improvement remains relevant across industries, education, and personal development.
Adopting Kaizen requires a mindset shift toward incremental progress. Organizations and individuals alike can begin by identifying areas for improvement, fostering a culture of learning, and embracing iterative change.
The future of Kaizen lies in its integration into daily habits and organizational cultures. By prioritizing small, consistent improvements, individuals and businesses can achieve long-term success and adaptability.
16. FAQ’S
1. What is Kaizen?
Kaizen is a Japanese philosophy that focuses on continuous, incremental improvement in all aspects of work and personal life. It aims to enhance efficiency, eliminate waste, and foster a culture of collaboration and innovation.
2. How does Kaizen differ from Lean and Six Sigma?
While Lean focuses on waste reduction and Six Sigma emphasizes quality control through statistical analysis, Kaizen is a broader philosophy that encourages small, continuous improvements in every area of an organization. It complements both methodologies rather than competing with them.
3. What are the core principles of Kaizen?
The key principles include:
- Continuous improvement through small, incremental changes
- Eliminating waste and maximizing efficiency
- Employee involvement and a team-oriented approach
- Standardization to sustain improvements
- Data-driven decision-making to ensure measurable progress
4. How can businesses implement Kaizen effectively?
Businesses can implement Kaizen by:
- Encouraging employee participation in identifying inefficiencies
- Using tools like PDCA (Plan-Do-Check-Act) for structured problem-solving
- Standardizing successful changes for long-term improvements
- Fostering a culture where every small improvement is valued and recognized
5. What are the benefits of Kaizen?
Some of the major benefits of Kaizen include:
- Improved productivity and efficiency
- Reduced operational costs and waste
- Higher employee engagement and morale
- Enhanced customer satisfaction
- A culture of continuous learning and innovation
6. What are the challenges in adopting Kaizen?
Common challenges include:
- Resistance to change from employees and management
- Short-term cost concerns before long-term benefits materialize
- Lack of leadership commitment to sustain improvements
- Difficulty in measuring progress for certain non-quantifiable changes
7. Can Kaizen be applied outside of manufacturing?
Yes, Kaizen is widely used in healthcare, education, software development, customer service, and even personal development. The philosophy applies to any field that values continuous improvement.
8. How does Kaizen improve employee engagement?
Kaizen fosters a participatory work environment where employees are encouraged to contribute ideas for process improvements. This sense of ownership boosts morale, motivation, and overall job satisfaction.
9. How does Kaizen apply to personal development?
In personal life, Kaizen helps individuals achieve goals by making small, consistent improvements over time. Whether it’s improving fitness, learning a new skill, or enhancing productivity, gradual progress leads to long-term success.
10. What are some real-world examples of Kaizen in action?
- Toyota: The company became a global leader in efficiency and quality by embedding Kaizen into its operations.
- Hospitals: Many healthcare institutions use Kaizen to reduce patient wait times and improve medical procedures.
- Tech Companies: Companies like Amazon and Google use Kaizen-inspired continuous improvement to enhance customer experience and streamline logistics.
11. Is Kaizen a one-time initiative or an ongoing process?
Kaizen is an ongoing process, not a one-time initiative. Its core idea is that improvement is continuous and should become part of an organization’s or individual’s daily routine.
12. How do small businesses and startups benefit from Kaizen?
Startups and small businesses can use Kaizen to improve efficiency, optimize resources, and enhance customer service without requiring large investments. Small, incremental changes can lead to sustainable growth over time.