1. Introduction
The pulley is a fundamental mechanical device that has been integral to human civilization for centuries. It operates on the principle of redirecting force to facilitate the movement of heavy loads with minimal effort. like gears and chain sprockets pulleys are used to transform from one shaft to another. Pulleys have found applications in various domains, from simple lifting mechanisms in ancient times to sophisticated industrial and engineering systems today. This article delves into the history, mechanics, classifications, Types of pulleys, and specialized applications of pulleys, along with their advantages and disadvantages.
2. History and Evolution of Pulleys
Pulleys date back to ancient civilizations, where they were employed in rudimentary lifting systems. The Egyptians, for instance, are believed to have used basic pulley systems to construct the pyramids, enabling them to hoist massive stone blocks into place. Similarly, the Greeks and Romans refined pulley technology, incorporating it into cranes and other lifting mechanisms that facilitated construction and transportation.
2.2 The Role of Pulleys in the Industrial Revolution
The Industrial Revolution marked a turning point in pulley usage. With the advent of mechanization, pulleys became integral to steam engines, textile mills, and large-scale manufacturing processes. The introduction of belt-driven machinery allowed for the efficient transfer of power across different mechanical components, significantly enhancing productivity and automation.
2.3 Modern Applications of Pulleys in Engineering
Today, pulleys are indispensable in various engineering fields. They are extensively used in automotive systems, elevators, cranes, conveyor belts, and gym equipment. Advancements in material science and precision engineering have further optimized pulley efficiency, reducing energy loss and enhancing durability.
3. Basic Mechanics of a Pulley System
3.1 Understanding the Physics of Pulleys
A pulley system consists of a wheel with a grooved rim, through which a rope, belt, or chain runs. When force is applied, the wheel rotates, altering the direction of the applied force. This mechanism reduces the amount of force needed to lift a load, making it easier to move heavy objects.
3.2 How Pulleys Reduce Effort and Increase Efficiency
The primary function of a pulley is to distribute force more effectively. By incorporating multiple pulleys, the load can be distributed over a greater distance, reducing the amount of force required to lift an object. This principle is commonly utilized in block and tackle systems, where multiple pulleys work in tandem to amplify lifting power.
3.3 The Role of Mechanical Advantage in Pulley Systems
Mechanical advantage (MA) refers to the ratio of output force to input force in a mechanical system. In pulley configurations, the mechanical advantage increases with the number of pulleys used. For instance, a single fixed pulley provides no mechanical advantage, whereas a system with multiple movable pulleys significantly reduces the effort needed to lift a load.
4. Classification of Pulleys Based on Function
4.1 Fixed Pulleys
A fixed pulley is anchored in place, meaning it does not move with the load. It changes the direction of force but does not reduce the effort required to lift an object. These pulleys are commonly found in flagpoles, window blinds, and well systems.
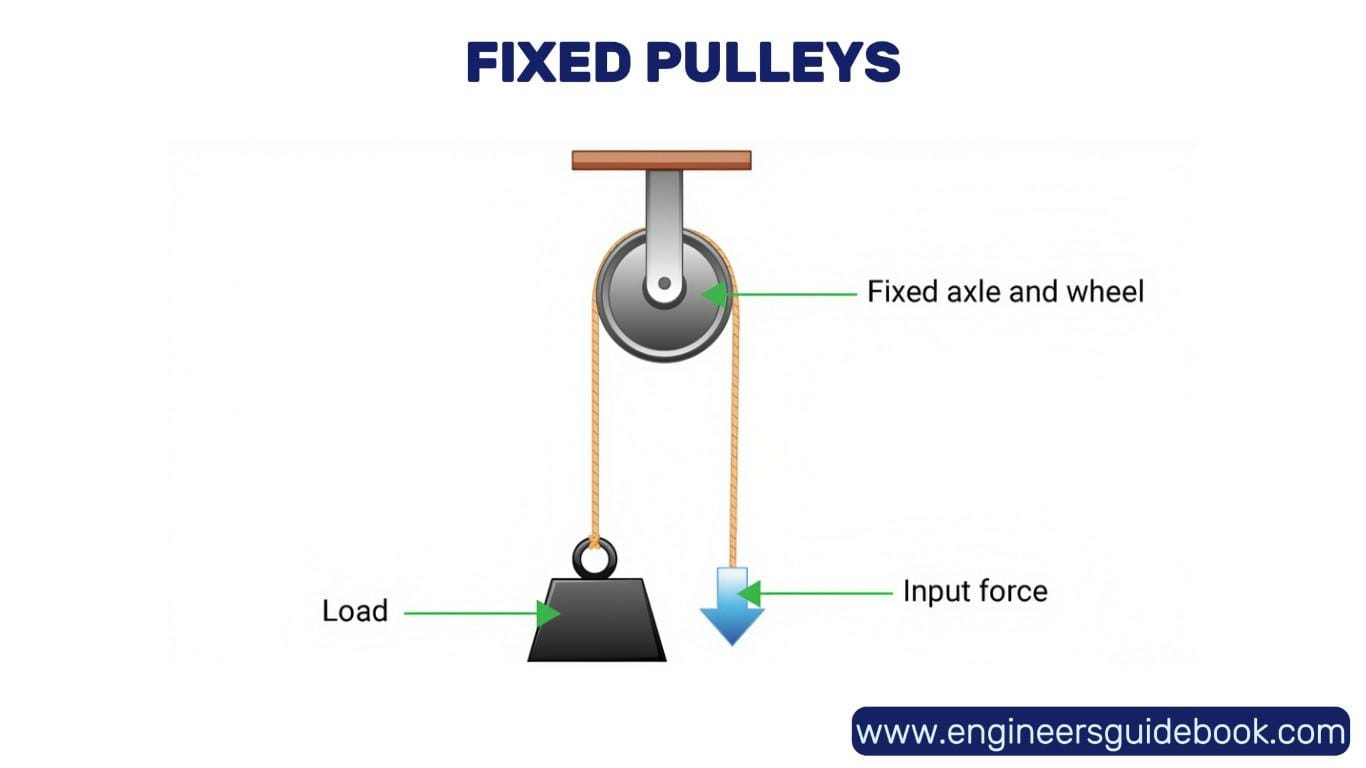
4.2 Movable Pulleys
Movable pulleys are attached to the load being lifted, allowing them to move along with it. This type of pulley effectively reduces the force required by distributing weight more evenly. Movable pulleys are widely used in construction hoists and rock climbing systems.
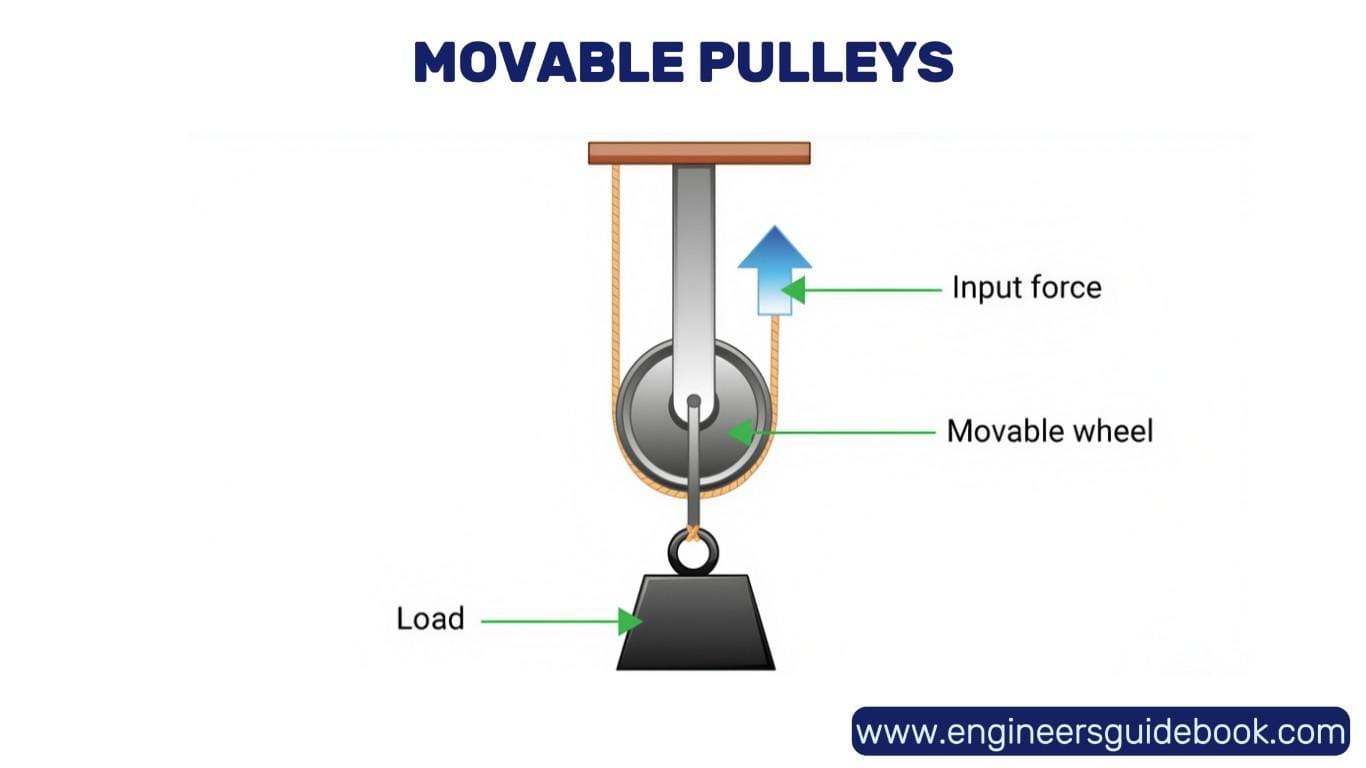
4.3 Compound Pulleys
A compound pulley system integrates both fixed and movable pulleys, combining their advantages. This arrangement provides significant mechanical advantage, making it easier to lift heavy loads with minimal effort. Compound pulleys are frequently used in cranes, ship rigging, and industrial lifting equipment.
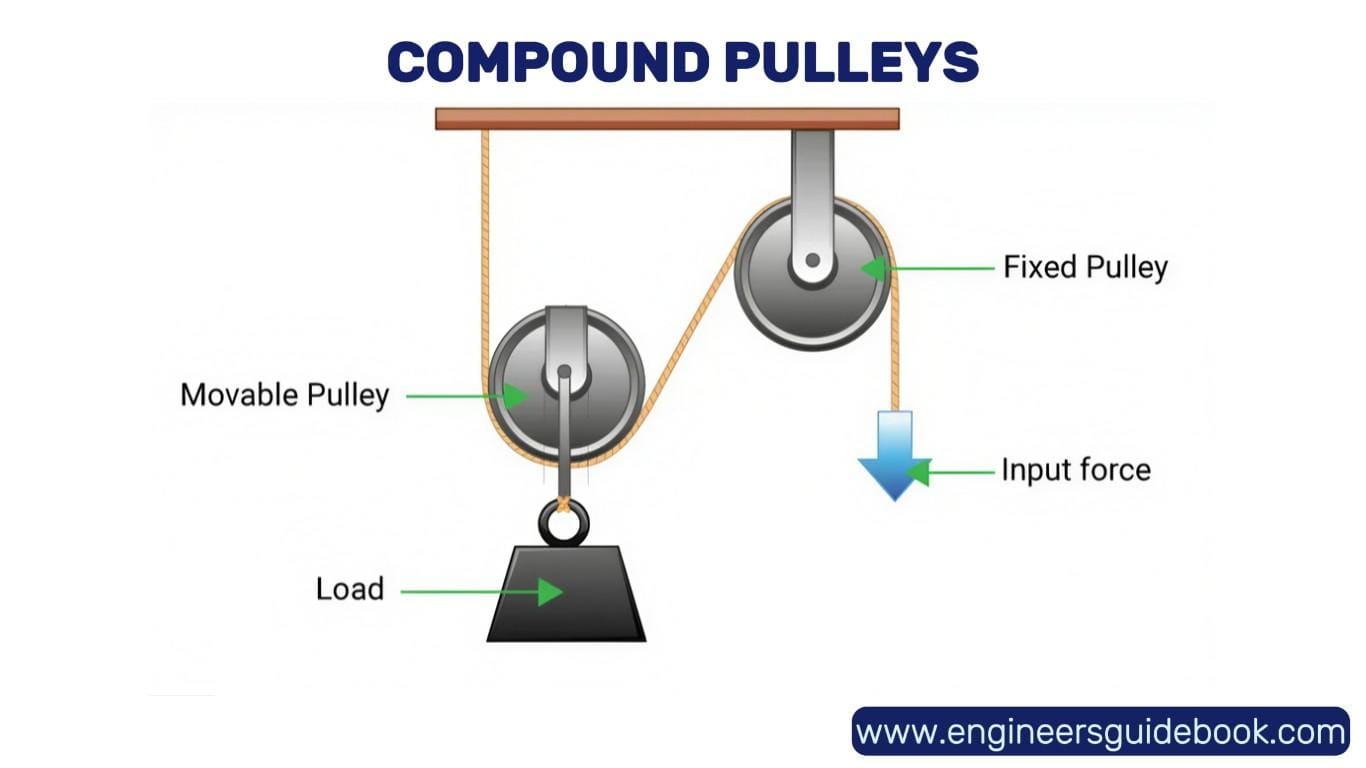
5. Types of Pulleys Based on Design and Structure
5.1 Grooved Pulleys
Grooved pulleys, also known as sheave pulleys, feature a channel along their circumference to securely guide a rope or belt. These pulleys enhance traction and prevent slippage, making them ideal for high-tension applications such as elevators and cable cars.
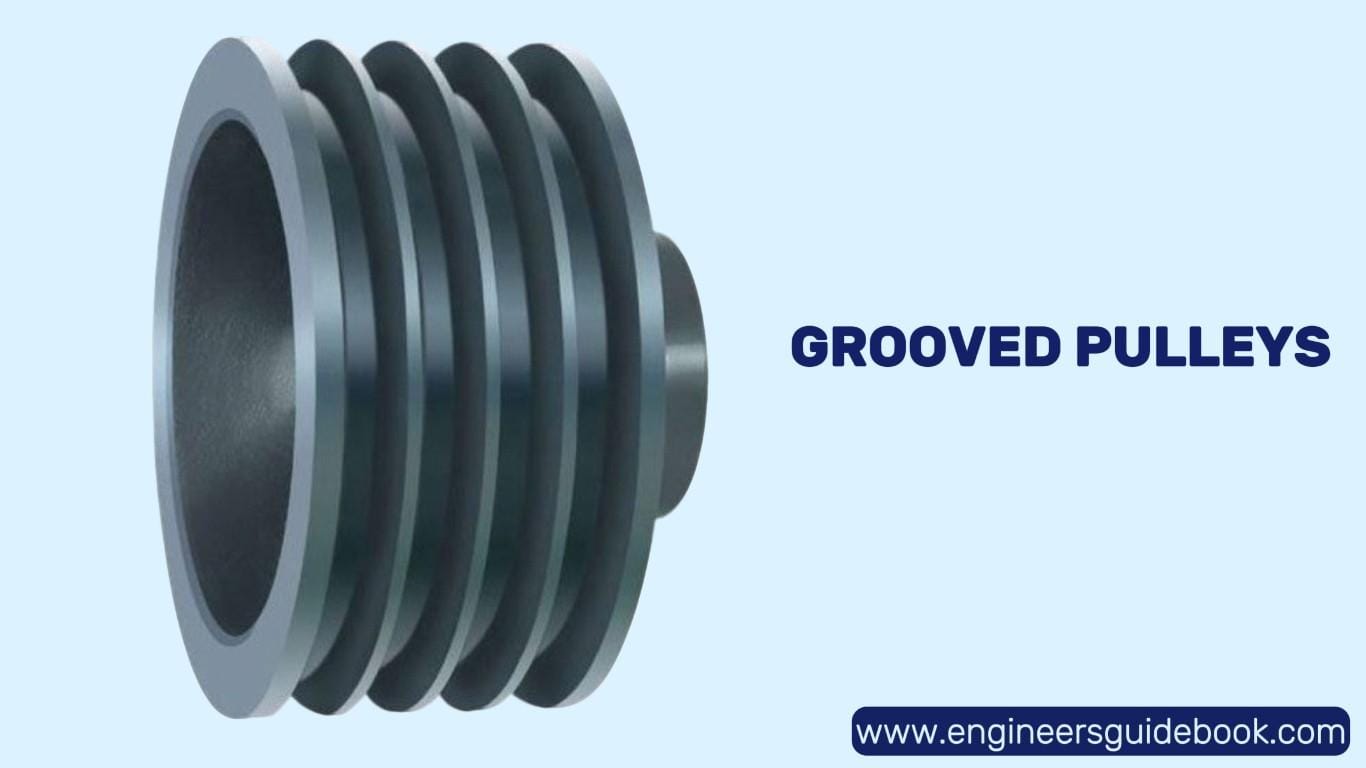
5.2 V-Belt Pulleys
V-belt pulleys are designed with a V-shaped groove that accommodates V-belts, which are commonly used in engines and machinery for efficient power transmission. The increased surface contact between the belt and pulley enhances grip, minimizing energy loss due to slippage.
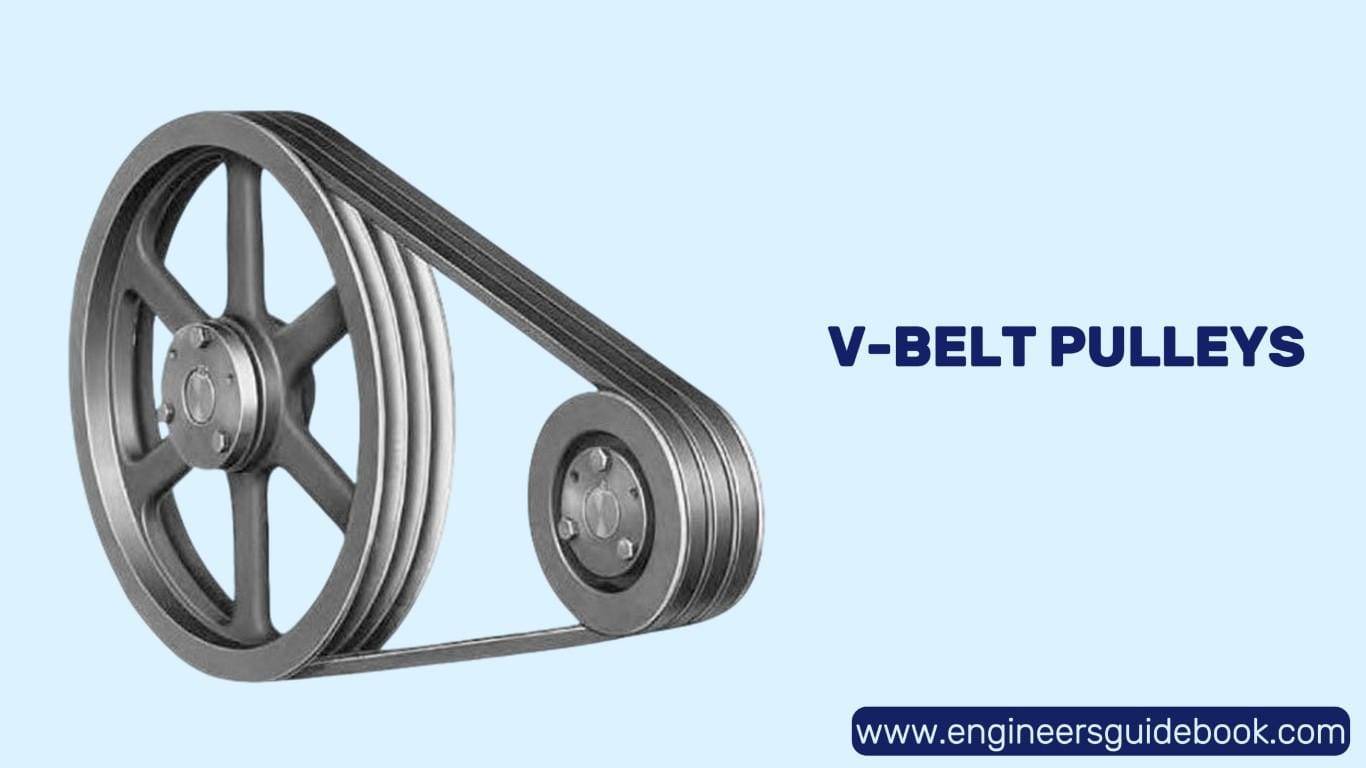
5.3 Timing Belt Pulleys
Timing belt pulleys feature evenly spaced teeth that mesh with a corresponding timing belt. This configuration ensures synchronized motion, making them essential in automotive camshaft systems, robotic arms, and industrial automation.

5.4 Flat Belt Pulleys
Flat belt pulleys have a smooth surface and are used with flat belts to transfer power between shafts. While less efficient than V-belt or timing belt pulleys, they are still used in applications where minimal friction and low-speed operation are required, such as in textile mills and old-fashioned lathes.
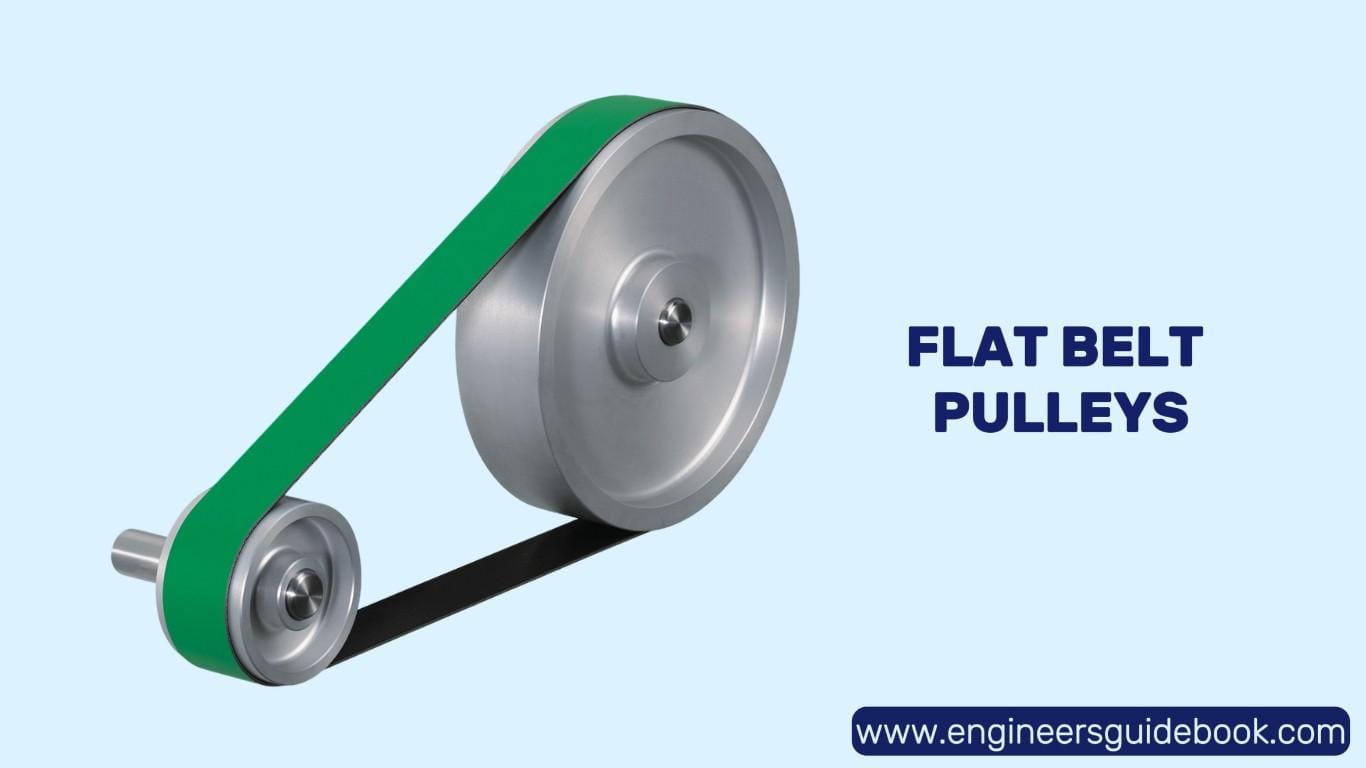
6. Specialized Pulleys for Industrial Applications
6.1 Magnetic Pulleys
Magnetic pulleys incorporate powerful magnets that attract ferrous materials, making them useful in conveyor systems for metal separation. These pulleys are widely used in recycling plants and mining operations to remove unwanted metal contaminants.
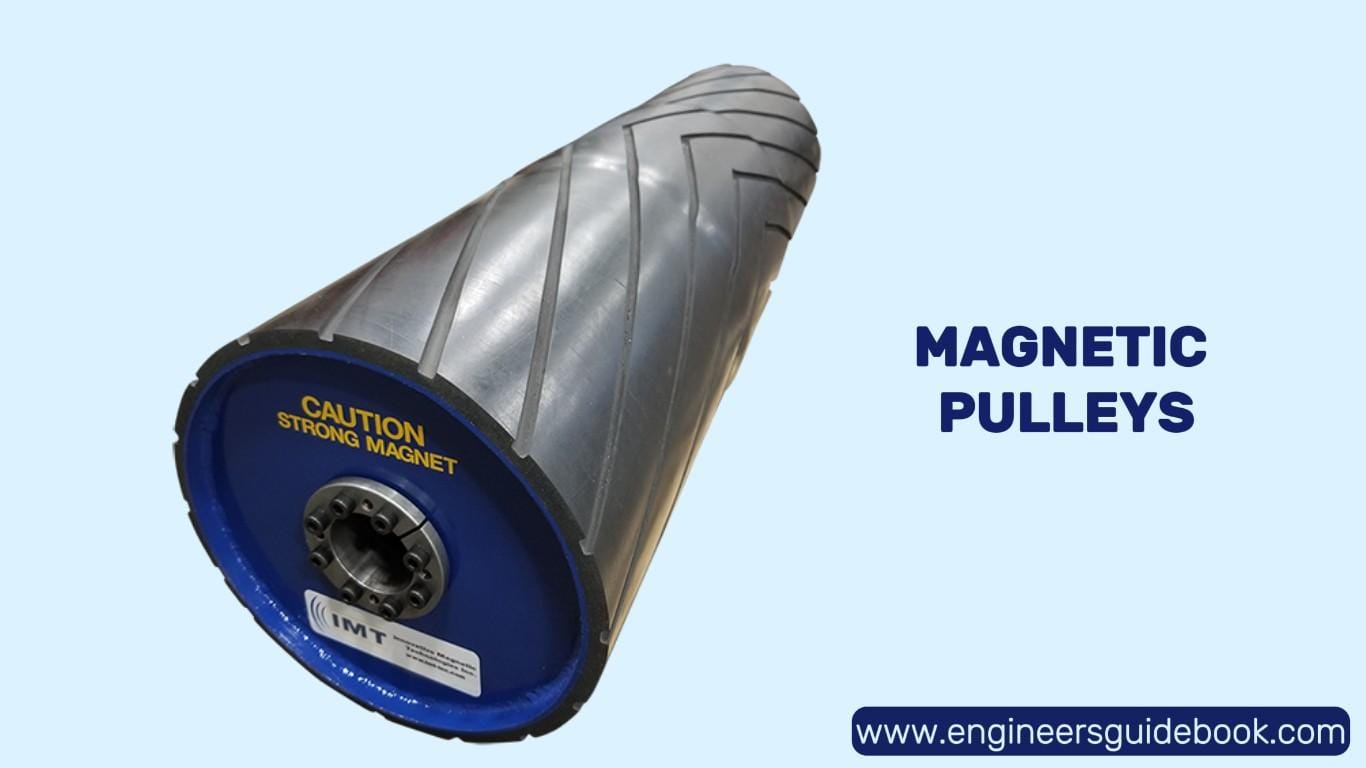
6.2 Snub Pulleys
Snub pulleys are auxiliary pulleys positioned close to the main drive pulley to increase the belt’s wrap angle. This additional contact enhances friction and prevents slippage, improving torque transmission in high-power applications such as conveyor belts and industrial machinery.

6.3 Idler Pulleys
Idler pulleys serve to guide and maintain tension in a belt system without transmitting power. These pulleys are commonly used in automotive serpentine belt systems and industrial conveyor setups to ensure smooth and consistent belt operation.
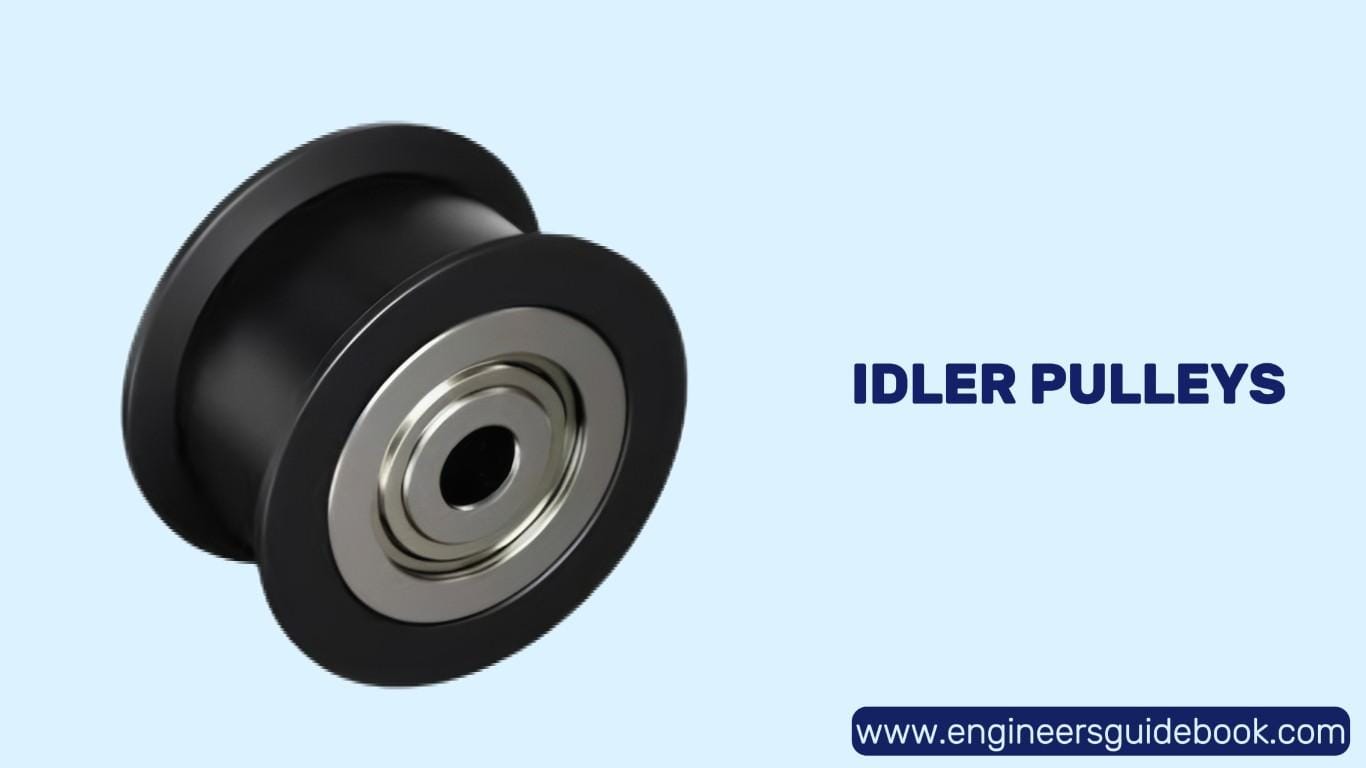
6.4 Step Pulleys
Step pulleys consist of multiple diameter steps along their circumference, allowing users to adjust the belt position for different speed settings. These pulleys are prevalent in drill presses, milling machines, and other equipment requiring variable-speed control.
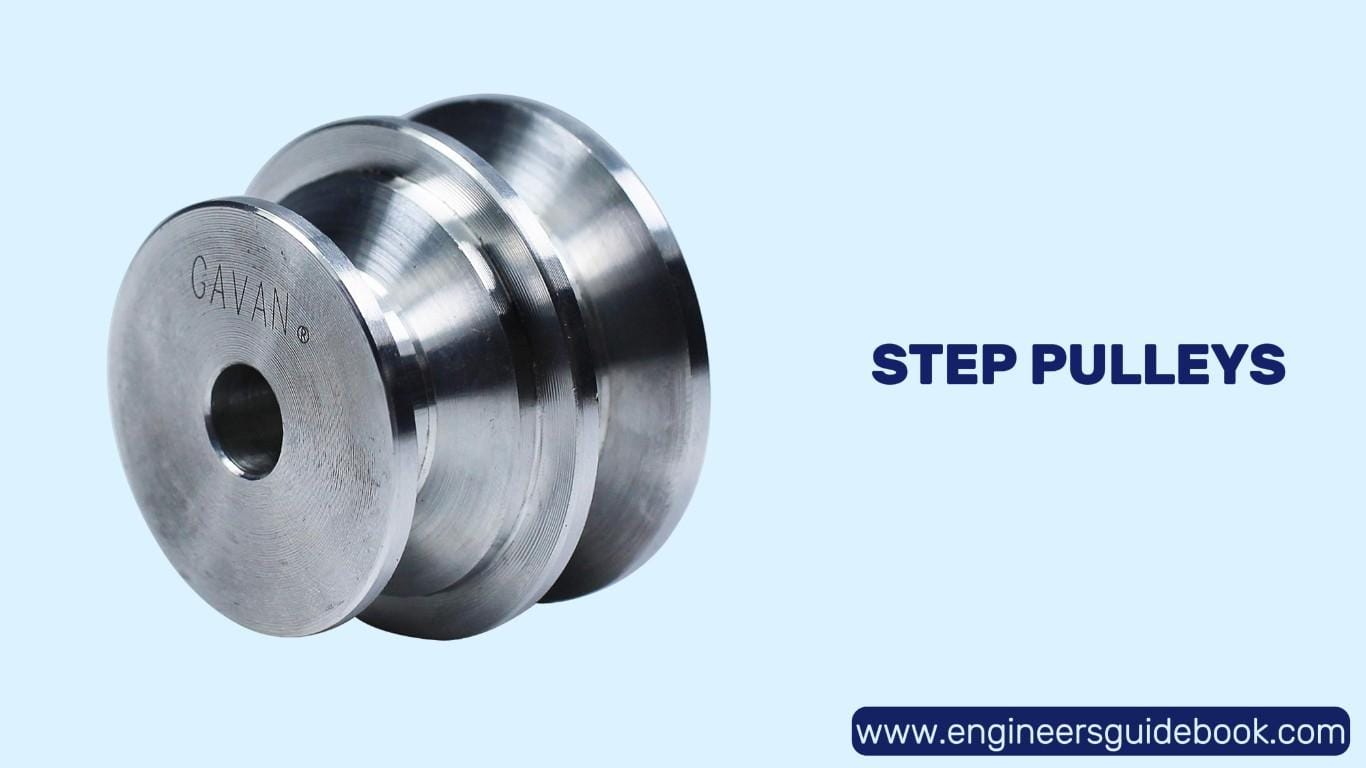
By understanding the diverse types of pulleys and their functionalities, industries can optimize mechanical systems for improved efficiency and performance.
7. Material Composition of Pulleys
7.1 Steel Pulleys
Steel pulleys are widely used in heavy-duty applications due to their superior strength and longevity. They can withstand high loads and extreme operating conditions, making them ideal for industrial machinery, automotive systems, and construction equipment. Additionally, steel pulleys exhibit excellent resistance to wear and deformation, ensuring long-term performance. However, they are susceptible to corrosion if not properly coated or maintained.
7.2 Aluminum Pulleys
Aluminum pulleys provide a balance between strength and weight, making them an excellent choice for applications requiring reduced mass. Their natural resistance to corrosion makes them ideal for marine environments, aerospace industries, and automotive systems. Moreover, aluminum pulleys enhance efficiency in high-speed applications due to their lower inertia. However, they may not be as strong as steel and can deform under excessive loads.
7.3 Plastic Pulleys
Plastic pulleys are commonly used in consumer products and low-load applications due to their affordability and versatility. They are lightweight, resistant to corrosion, and require minimal maintenance. Modern engineering plastics, such as nylon and polycarbonate, offer improved durability and friction resistance. However, plastic pulleys may not be suitable for high-temperature or heavy-duty applications due to their limited load-bearing capacity.
7.4 Composite Pulleys
Composite pulleys incorporate advanced materials like carbon fiber or reinforced polymers to combine the best properties of traditional materials. These pulleys offer high strength-to-weight ratios, enhanced resistance to wear, and superior performance in specialized environments. They are commonly used in aerospace, high-performance automotive systems, and industrial robotics. Despite their advantages, composite pulleys can be expensive and may require precise manufacturing processes.
8. Advantages of Using Pulleys in Mechanical Systems
8.1 Reducing the Force Required for Lifting
Pulleys allow for the efficient lifting of heavy loads by distributing force through mechanical advantage. This reduction in required effort makes tasks easier and more manageable, particularly in cranes, hoists, and lifting mechanisms.
8.2 Enhancing Load Distribution and Stability
By evenly distributing weight across multiple points, pulleys enhance stability and reduce strain on individual components. This is crucial in applications like suspension bridges and conveyor systems, where balanced load distribution ensures operational safety.
8.3 Increasing Efficiency in Power Transmission
Pulleys enable smooth power transmission by converting rotational energy into linear motion. This efficiency is critical in belt-driven systems, where pulleys facilitate energy transfer with minimal energy loss, thereby improving performance.
8.4 Minimizing Wear and Tear on Components
Properly designed pulley systems reduce direct stress on components, leading to increased longevity of machinery. By reducing friction and distributing loads effectively, pulleys contribute to lower maintenance costs and enhanced durability.
9. Disadvantages and Limitations of Pulley Systems
9.1 Friction and Energy Loss
While pulleys improve mechanical advantage, they also introduce friction between the belt or rope and the pulley surface. This can lead to energy losses and reduced overall system efficiency, necessitating careful material selection and lubrication.
9.2 Space Requirements
Complex pulley arrangements, such as block and tackle systems, require significant space. In environments with spatial constraints, integrating pulley systems can be challenging and may necessitate alternative mechanical solutions.
9.3 Maintenance and Lubrication Challenges
Pulleys, especially those used in high-load applications, require regular maintenance to ensure smooth operation. Bearings, belts, and cables must be inspected, lubricated, and occasionally replaced to prevent system failures.
9.4 Load Capacity Limitations
Although pulleys distribute load efficiently, they still have inherent limitations regarding maximum weight capacity. Exceeding these limits can lead to belt slippage, rope failure, or structural damage, requiring careful load calculations.
10. Pulley Systems in Everyday Life
10.1 The Role of Pulleys in Elevators and Lifts
Elevators rely on sophisticated pulley systems to move cabins up and down smoothly. Counterweights, cables, and motor-driven pulleys work together to provide efficient and safe vertical transportation.
10.2 Pulleys in Gym Equipment
Exercise machines incorporate pulley systems to adjust resistance levels, enabling controlled movements and targeted muscle engagement. Adjustable pulleys allow users to modify angles and tension for diverse workout routines.
10.3 How Pulleys Function in Bicycles
Bicycles use pulley-like mechanisms in derailleur systems to change gears smoothly. Similarly, automobile engines employ pulley-driven belts to power essential components such as alternators and air conditioning compressors.
10.4 Use of Pulleys in Home Appliances
Household appliances, including washing machines and ceiling fans, incorporate pulleys to transfer motion efficiently. These mechanisms reduce motor strain and enhance operational lifespan.
11. Pulleys in Heavy-Duty Industrial Applications
11.1 Mining and Construction
In mining and construction, pulleys play a crucial role in lifting and transporting heavy materials. Wire rope pulleys in cranes and hoists ensure safe and efficient movement of loads in demanding environments.
11.2 Marine and Shipping
Ships and port facilities utilize pulley systems to maneuver cargo, control sails, and operate winches. These mechanisms enhance load management and optimize maritime logistics.
11.3 Manufacturing and Assembly Lines
Pulleys form the backbone of conveyor belt systems used in manufacturing plants. They facilitate continuous material transport, ensuring seamless workflow and high productivity.
12. Innovations in Pulley Technology
12.1 Smart Pulleys with Sensors for Load Monitoring
Advanced pulleys are now equipped with sensors to monitor load distribution, wear, and operational efficiency in real-time. These innovations improve safety and predictive maintenance strategies.
12.2 Advanced Coatings for Reduced Friction and Wear
Modern pulleys incorporate advanced coatings like Teflon and ceramic composites to minimize friction and enhance durability. These improvements contribute to higher efficiency and reduced maintenance requirements.
12.3 High-Efficiency Pulleys in Energy-Saving Systems
Energy-efficient pulley designs optimize mechanical systems by reducing energy consumption. Industries are increasingly adopting these pulleys to improve sustainability and lower operational costs.
13. Comparison of Pulley Systems with Other Mechanical Devices
13.1 Pulleys vs. Gears
Pulleys and gears are both essential mechanical components used for motion transfer, yet they operate on fundamentally different principles. Pulleys rely on belts or ropes to transmit force, offering smooth and silent operation with minimal energy loss. Gears, on the other hand, function through interlocking teeth that provide direct torque transmission. While pulleys excel in long-distance power transmission and reduced mechanical wear, gears offer superior precision and torque control. The choice between the two depends on the application’s requirements, such as efficiency, load capacity, and operational complexity.
13.2 Pulleys vs. Levers
Levers and pulleys both function as simple machines designed to reduce effort, yet their mechanisms differ significantly. A lever operates around a fixed fulcrum, magnifying force through mechanical advantage, making it ideal for applications requiring direct force application, such as crowbars or seesaws. Pulleys, however, provide continuous force distribution over a longer distance, making them preferable in lifting and tensioning applications, such as cranes and conveyor belts. When selecting between these two, one must consider the nature of the mechanical task—whether a fixed pivot point or continuous motion is required.
13.3 Pulleys vs. Hydraulic Lifting Mechanisms
Hydraulic lifting mechanisms employ fluid pressure to generate immense lifting force, whereas pulleys depend on mechanical advantage to facilitate movement. Hydraulics offer superior load-bearing capabilities, making them ideal for industrial applications requiring precision and immense lifting power, such as forklifts and heavy-duty presses. Pulleys, however, provide a simpler, energy-efficient alternative without the complexity of pressurized systems. While hydraulics require regular maintenance to prevent leaks and fluid degradation, pulleys demand minimal upkeep, making them cost-effective in lower-load applications.
Feature | Pulleys | Gears | Levers | Hydraulic Lifting Mechanisms |
---|---|---|---|---|
Function | Uses belts or ropes to transmit force | Uses interlocking teeth to transfer torque | Operates around a fulcrum to magnify force | Uses pressurized fluid to generate lifting power |
Efficiency | Smooth and low energy loss | High precision but increased mechanical wear | Direct force application | High efficiency for heavy loads |
Best Application | Long-distance power transmission | High torque and precision control | Short-distance force magnification | Industrial lifting and material handling |
Maintenance | Minimal upkeep | Requires lubrication and precise alignment | Low maintenance | Requires regular checks for leaks and fluid degradation |
14. How to Select the Right Pulley for Your Needs
14.1 Evaluating Load Requirements and Safety Factors
Selecting the appropriate pulley begins with understanding the load capacity it must handle. Load ratings must account for static and dynamic forces, ensuring that the pulley can withstand operational stresses without failure. Safety factors, such as potential shock loads, must also be considered to prevent premature wear or structural failure. Engineers often use a margin of safety to ensure reliability in high-stress environments, making load assessment a crucial step in pulley selection.
14.2 Choosing the Right Material for Durability and Performance
The material composition of a pulley plays a pivotal role in its longevity and functionality. Steel pulleys are preferred for high-strength applications, while aluminum variants offer lightweight benefits with corrosion resistance. Composite pulleys, made from reinforced polymers or fiber-reinforced materials, provide an optimal balance of strength, weight, and durability for specialized applications. The right material selection ensures that the pulley performs optimally within its intended operational environment.
14.3 Considering Space Constraints and System Efficiency
Space limitations are a critical consideration in pulley system design. Compact machinery may require smaller-diameter pulleys or idler pulleys to fit within tight configurations. Additionally, system efficiency depends on factors such as belt alignment, friction reduction, and rotational inertia. Selecting a pulley with appropriate groove profiles and belt compatibility enhances overall efficiency and minimizes energy losses, ensuring smooth operation in mechanical systems.
15. Maintenance and Troubleshooting of Pulley Systems
15.1 Common Issues in Pulley Operation and Their Solutions
Pulley systems, while reliable, are susceptible to common issues such as misalignment, belt slippage, and excessive wear. Misalignment can lead to uneven force distribution, causing inefficiencies and potential failure. Belt slippage may result from inadequate tension, requiring periodic adjustments or the use of tensioning pulleys. Excessive wear often indicates improper lubrication or contamination, necessitating routine inspections and maintenance.
15.2 Best Practices for Lubrication and Preventive Maintenance
Proper lubrication reduces friction and extends the lifespan of pulley components. Depending on the material, different lubrication methods may be required, such as oil-based lubricants for metal pulleys and dry lubricants for composite or plastic variants. Preventive maintenance schedules should include belt tension checks, alignment verification, and contamination removal to ensure optimal performance and longevity.
15.3 Signs of Wear and When to Replace a Pulley
Recognizing wear indicators is crucial for maintaining system efficiency. Signs such as excessive noise, visible surface wear, cracks, or belt degradation indicate that a pulley may need replacement. Regular inspections help identify wear before catastrophic failure occurs, reducing downtime and preventing costly system damage. Engineers often implement predictive maintenance strategies, such as vibration analysis, to monitor pulley health and ensure timely replacements.
16. Conclusion
Pulleys remain indispensable components in mechanical engineering, offering versatility, efficiency, and reliability across various applications. From simple lifting mechanisms to advanced industrial machinery, their role in reducing effort and optimizing force distribution is invaluable. Understanding the different types of pulleys, their material compositions, advantages, and limitations allows for informed selection and proper maintenance. By integrating modern innovations and best practices, pulley systems can continue to evolve, enhancing mechanical efficiency in diverse engineering fields.
17. FAQs
1. What is the primary function of a pulley in a mechanical system?
A pulley is designed to change the direction of force and reduce the effort required to lift or move a load. It operates on the principle of mechanical advantage, distributing force efficiently across a system to enhance lifting, tensioning, or power transmission.
2. What are the different types of pulleys and their uses?
Pulleys are classified into several types based on function and design:
- Fixed Pulleys: Used in flagpoles and well systems to redirect force.
- Movable Pulleys: Found in cranes and hoists to reduce effort.
- Compound Pulleys: Combine fixed and movable pulleys for greater mechanical advantage.
- Grooved Pulleys: Used in belt-driven machinery for efficient power transmission.
- Timing Belt Pulleys: Ensure precise motion in engines and automation systems.
3. How does a pulley reduce the effort needed to lift heavy loads?
A pulley system distributes weight across multiple ropes or belts, reducing the direct force needed to lift an object. By increasing the number of pulleys in a system (such as a block and tackle), the mechanical advantage increases, allowing heavier loads to be lifted with minimal effort.
4. What materials are pulleys commonly made from?
Pulleys are made from a variety of materials, depending on the application:
- Steel: Used in heavy-duty industrial applications due to its strength and durability.
- Aluminum: Preferred in aerospace and automotive industries for its lightweight and corrosion resistance.
- Plastic: Found in household appliances and light-duty applications due to its affordability and flexibility.
- Composite Materials: Used in specialized fields for their enhanced strength-to-weight ratio and reduced friction.
5. What are the advantages of using pulleys in machinery?
Pulleys provide several benefits, including:
- Reduction in required lifting force through mechanical advantage.
- Smooth and continuous motion transmission in power-driven systems.
- Even distribution of load, preventing excessive stress on individual components.
- Versatility in application, from simple hand-operated devices to complex industrial machines.
6. What are the common problems encountered in pulley systems?
Pulley systems can face issues such as:
- Belt slippage due to inadequate tension or wear.
- Misalignment, leading to inefficiencies and excessive wear.
- Frictional losses, reducing overall energy efficiency.
- Component degradation, requiring periodic maintenance and replacements.
7. How do pulleys compare to gears and hydraulic lifting mechanisms?
Pulleys are ideal for long-distance power transmission and simple load-lifting mechanisms, whereas gears provide direct torque transmission for high-precision applications. Hydraulic lifting systems, on the other hand, are used for heavy-duty lifting but require pressurized fluids and regular maintenance, making them more complex than pulley-based lifting solutions.
8. How can pulley systems be maintained for long-term efficiency?
Regular maintenance ensures longevity and optimal performance, including:
- Periodic lubrication to reduce friction and prevent wear.
- Tension adjustments to prevent belt slippage.
- Alignment checks to ensure smooth operation.
- Timely replacement of worn-out components to avoid system failures.