1. Introduction
1.1 The Importance of Process Optimization in Modern Industries
Process optimization has become a critical determinant of an organization’s success in an era characterized by rapid technological advancements and increasing market competition. Efficiency is no longer a luxury but a necessity to maintain a competitive edge. Industries, whether in manufacturing, healthcare, logistics, or software development, must continuously refine their workflows to eliminate inefficiencies, reduce costs, and improve product quality.
Process optimization enhances productivity and fosters sustainability by minimizing resource waste and improving energy efficiency. Businesses that fail to streamline operations risk stagnation, higher operational costs, and a decline in customer satisfaction. As industries move toward digital transformation, leveraging systematic tools to refine processes is indispensable.
1.2 How Value Stream Mapping Enhances Efficiency and Productivity
Value Stream Mapping (VSM) is one such tool that empowers organizations to visualize, analyze, and optimize their processes. By offering a graphical representation of material and information flows, VSM identifies inefficiencies such as bottlenecks, redundant steps, and excessive lead times. Unlike traditional process analysis methods, VSM provides a holistic perspective, enabling organizations to target areas for substantial improvements.
Through VSM, businesses can design streamlined workflows that reduce delays, improve throughput, and enhance overall productivity. The method not only addresses operational inefficiencies but also fosters a culture of continuous improvement. Employees gain clarity on how their roles contribute to the value chain, leading to more engaged and proactive teams.
2. Understanding Value Stream Mapping
2.1 Definition and Core Principles of Value Stream Mapping
Value Stream Mapping is a lean-management technique used to analyze, design, and improve the flow of materials and information required to deliver a product or service to the customer. At its core, VSM revolves around the identification of value-added and non-value-added activities, enabling organizations to focus on creating efficient and waste-free processes.
The primary principles of VSM include:
- Eliminating Waste: Identifying and removing non-value-adding steps that contribute to inefficiencies.
- Focusing on Customer Value: Aligning processes to deliver what customers truly need in the most efficient way.
- Optimizing Flow: Ensuring smooth transitions between process stages, minimizing delays and redundancies.
- Continuous Improvement: Using VSM as a dynamic tool that evolves with changing business needs and customer demands.
By adhering to these principles, organizations can refine their operations, enhance their value delivery, and maintain a competitive advantage.

2.2 The Role of VSM in Lean Manufacturing and Continuous Improvement
Lean manufacturing is a methodology that aims to minimize waste while maximizing value. Within this framework, VSM serves as a fundamental tool for identifying inefficiencies and implementing targeted improvements. By mapping out the entire production or service delivery process, organizations can pinpoint areas where delays, excess inventory, or unnecessary processing occur.
In the context of continuous improvement, VSM provides a structured approach to process optimization. Unlike one-time process redesigns, it facilitates ongoing refinements through iterative analysis and enhancements. Organizations that integrate VSM into their continuous improvement initiatives benefit from greater agility, enhanced quality, and sustained operational efficiency.
3. Key Components of a Value Stream
3.1 Identifying Value-Adding and Non-Value-Adding Activities
A crucial step in value stream mapping is distinguishing between activities that contribute to customer value and those that do not. Value-adding activities are process steps that directly enhance the product or service in a way that the customer is willing to pay for. These include operations such as machining, assembling, and software coding, which transform raw materials or information into a finished product.
Non-value-adding activities, on the other hand, are actions that consume resources without improving the final output. These can be further classified into:
- Necessary Non-Value-Adding Activities: Tasks required by regulations or industry standards, such as quality inspections and compliance checks.
- Pure Waste: Activities such as excessive waiting time, unnecessary movement of materials, overproduction, and redundant paperwork that add no tangible value and should be eliminated.
By meticulously identifying these activities, organizations can streamline workflows, reduce costs, and enhance operational efficiency.

3.2 The Flow of Materials and Information in a Value Stream
A value stream consists of two primary flows: material flow and information flow. Understanding and optimizing both is critical to achieving operational excellence.
- Material Flow: This refers to the physical movement of raw materials, work-in-progress items, and finished products. Inefficiencies in material flow often manifest as excessive transportation, storage delays, or mismanaged inventory. By mapping out the material flow, businesses can restructure layouts, enhance logistics, and ensure just-in-time (JIT) production.
- Information Flow: This encompasses communication between various process stages, including work orders, production schedules, and customer feedback. Ineffective information flow leads to misaligned operations, delays, and errors. By improving information transparency and integrating real-time data tracking, organizations can enhance coordination and minimize disruptions.
Optimizing both flows is crucial to creating a seamless and efficient value stream that maximizes productivity and minimizes waste.
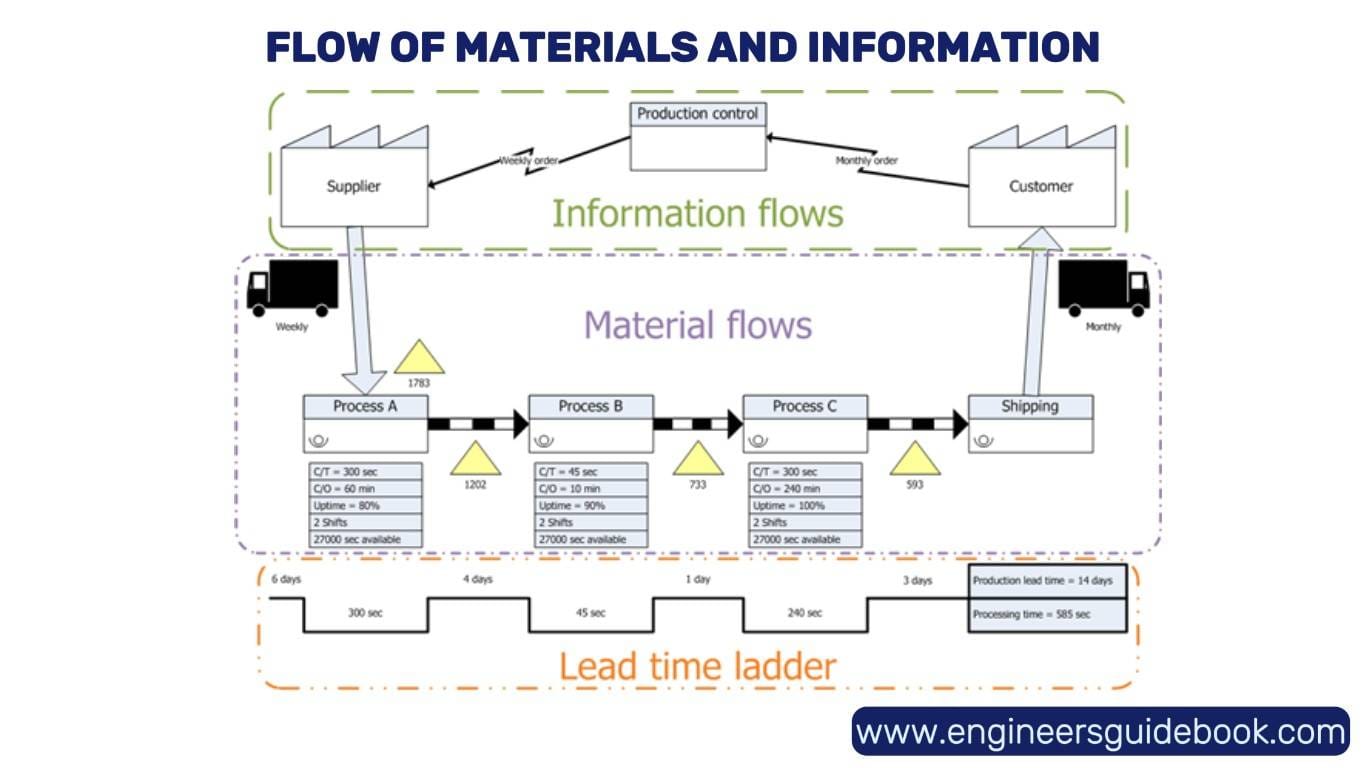
4. The Purpose and Benefits of Value Stream Mapping
4.1 How VSM Helps Identify Waste and Bottlenecks
One of the most significant advantages of Value Stream Mapping is its ability to expose inefficiencies that may otherwise remain hidden within daily operations. By visually mapping out each step in a process, VSM enables organizations to detect:
- Bottlenecks: Areas where workflow slows down due to excessive workloads, inefficient machinery, or procedural constraints.
- Excessive Lead Time: Delays in production or service delivery that impact customer satisfaction and increase holding costs.
- Overprocessing: Unnecessary steps that do not contribute to the final product’s value but consume time and resources.
- Defects and Rework: Errors that necessitate corrective actions, leading to wasted materials and time.
By addressing these inefficiencies, businesses can develop targeted strategies to enhance operational effectiveness and customer satisfaction.
4.2 Enhancing Workflow, Reducing Lead Time, and Improving Quality
Value Stream Mapping is a powerful tool for creating smoother, more efficient workflows. When properly implemented, VSM leads to:
- Reduced Lead Time: By eliminating unnecessary delays and streamlining production phases, organizations can accelerate delivery times without compromising quality.
- Improved Resource Allocation: A clear understanding of process inefficiencies enables better distribution of workforce, machinery, and materials.
- Enhanced Quality Control: By reducing errors and unnecessary handling, VSM contributes to more consistent, high-quality output.
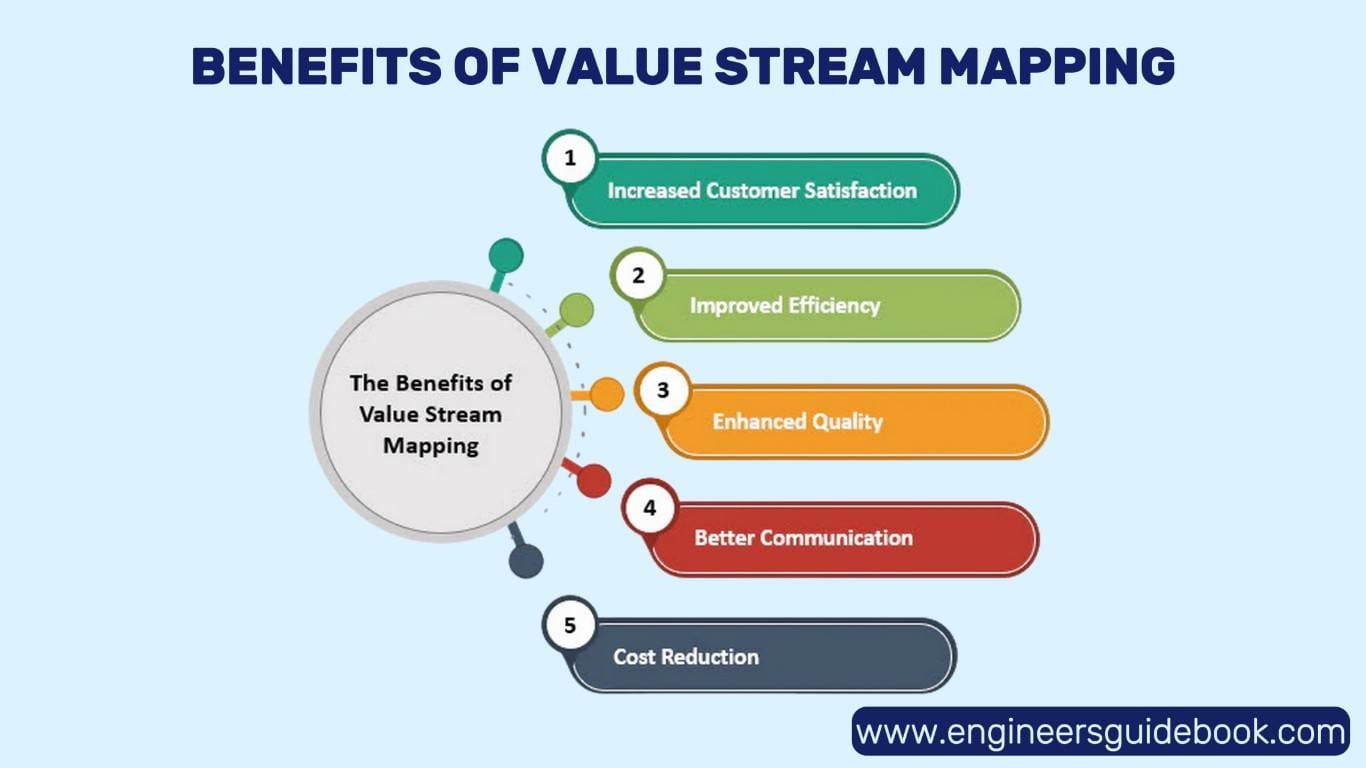
5. When and Where to Use Value Stream Mapping
Value Stream Mapping (VSM) is a powerful tool that applies across diverse industries and business environments. Its core function is to visualize processes, identify inefficiencies, and enhance workflow efficiency. However, knowing when and where to deploy VSM is essential to maximizing its impact.
5.1 Industries and Business Sectors That Benefit from VSM
While initially developed for manufacturing, Value Stream Mapping has found applications in multiple sectors, each leveraging its methodology to optimize performance:
- Manufacturing and Production – VSM plays a pivotal role in lean manufacturing by helping factories eliminate bottlenecks, reduce lead times, and minimize waste in material and labor usage.
- Healthcare – Hospitals and healthcare institutions utilize VSM to streamline patient flow, reduce waiting times, and optimize resource allocation in departments such as emergency rooms, operating theaters, and supply chains.
- Logistics and Supply Chain Management – Warehouses, distribution centers, and freight companies employ VSM to improve inventory management, enhance transportation efficiency, and eliminate redundancies in supply chain operations.
- Software Development and IT Services – Agile and DevOps teams use VSM to refine workflows, optimize software deployment pipelines, and enhance collaboration across development and operations.
- Service Industry and Administration – VSM aids businesses in financial services, customer support, and administrative workflows by reducing processing time, eliminating unnecessary steps, and improving service quality.
5.2 Situations Where VSM Can Drive Process Improvements
VSM proves most beneficial when organizations encounter inefficiencies that negatively impact performance. Key scenarios where VSM can drive meaningful process improvements include:
- High Lead Times – When excessive delays exist between different process stages, VSM can pinpoint root causes and streamline workflows.
- Excessive Waste and Redundancy – In organizations struggling with overproduction, excessive transportation, or unnecessary processing, VSM helps identify and eliminate waste.
- Resource Bottlenecks – Whether in manufacturing, service delivery, or IT, identifying constraints in resources (human, material, or technological) can lead to more efficient allocation.
- Frequent Errors and Rework – When defects or incorrect outputs lead to high levels of rework, VSM highlights problem areas and potential solutions.
- Scaling and Process Standardization – Businesses experiencing rapid growth can use VSM to standardize processes, ensuring consistent performance across multiple locations or teams.
6. The Key Symbols and Notations in VSM
To effectively create and interpret Value Stream Maps, it is crucial to understand the standardized symbols and notations that represent different process elements. These symbols provide a universally recognized language for depicting material flow, information flow, and process sequences.
6.1 Understanding the Standard Icons and Their Meanings
VSM employs a set of standard icons to represent various aspects of a process. Some of the most commonly used symbols include:
- Process Box – Represents a specific activity or operation within the value stream.
- Material Flow Arrows – Indicate the movement of raw materials, work-in-progress, or finished goods.
- Information Flow Arrows – Show communication and data exchange between different process stages.
- Inventory Triangle – Denotes inventory accumulation or storage points within the value stream.
- Kaizen Burst – Highlights areas where rapid improvement actions (Kaizen events) should be implemented.
- Timeline Bar – Depicts the time required for value-adding and non-value-adding activities, helping assess lead time and process delays.
6.2 How to Interpret VSM Diagrams Effectively
Interpreting a Value Stream Map requires a structured approach to identifying inefficiencies and improvement opportunities. Key considerations include:
- Analyzing Flow Direction – Understanding the sequence of steps and how materials and information move through the process.
- Identifying Bottlenecks – Examining areas where excessive waiting times, backlogs, or inventory accumulation occur.
- Distinguishing Between Value-Adding and Non-Value-Adding Activities – Differentiating steps that contribute to the final product or service from those that create waste.
- Assessing Cycle Times and Lead Times – Evaluating process durations to identify time-consuming stages that require optimization.

7. The Step-by-Step Process of Creating a Value Stream Map
Developing an effective Value Stream Map involves a systematic approach to mapping, analyzing, and optimizing a process.
7.1 Defining the Scope and Selecting the Process to Analyze
The first step in VSM is identifying the process or value stream to be mapped. It is essential to:
- Clearly define the boundaries of the analysis (e.g., production line, order fulfillment, or software deployment).
- Determine key objectives such as reducing waste, improving lead time, or enhancing efficiency.
- Gather input from stakeholders who are directly involved in the process.
7.2 Gathering Data and Understanding the Current State
To create an accurate representation of the existing process, organizations must collect detailed data, including:
- Process cycle times and lead times.
- Inventory levels and material flow rates.
- Communication and data transfer methods.
- Bottlenecks and sources of inefficiencies.
7.3 Mapping the Current State to Identify Inefficiencies
Once data is collected, a visual representation of the current state is created. This involves:
- Plotting each process step sequentially.
- Illustrating material and information flows using standard VSM symbols.
- Highlighting delays, waiting periods, and areas of excessive resource consumption.
7.4 Analyzing the Current State and Identifying Opportunities for Improvement
After mapping the current state, teams analyze inefficiencies and identify improvement opportunities:
- Categorizing waste (e.g., overproduction, defects, waiting time).
- Evaluating non-value-adding activities for potential elimination or optimization.
- Identifying areas where automation or process redesign could improve efficiency.
7.5 Designing the Future State for an Optimized Workflow
A future state map is created to depict the ideal workflow with enhanced efficiency and minimal waste. Key improvements may include:
- Reducing wait times and eliminating unnecessary steps.
- Enhancing information flow through automation or digitalization.
- Implementing lean manufacturing principles such as Just-in-Time (JIT) production.
7.6 Developing an Implementation Plan for Process Improvement
The final step involves translating the future state map into actionable changes:
- Prioritizing improvement initiatives based on impact and feasibility.
- Assigning responsibilities to process owners and team members.
- Establishing performance metrics to track progress and sustain improvements.

8. Common Mistakes to Avoid in Value Stream Mapping
While Value Stream Mapping is a highly effective tool, several common pitfalls can reduce its effectiveness.
8.1 Overcomplicating the Mapping Process
A common mistake is creating overly complex maps that include excessive detail, making them difficult to interpret and act upon. To avoid this:
- Focus on key process elements rather than mapping every minor detail.
- Keep symbols and notations consistent and straightforward.
- Ensure clarity by simplifying process flows where possible.
8.2 Failing to Involve Key Stakeholders and Team Members
Value Stream Mapping should be a collaborative process. Excluding key stakeholders can lead to:
- Incomplete or inaccurate representations of the actual process.
- Resistance to change due to a lack of involvement and buy-in.
- Missed improvement opportunities identified by frontline employees.
8.3 Ignoring Data-Driven Decision-Making
Effective VSM relies on empirical data rather than assumptions. Mistakes related to poor data analysis include:
- Relying on subjective observations instead of objective performance metrics.
- Making process changes without validating their impact through quantitative analysis.
- Failing to measure post-implementation performance improvements.
9. Tools and Software for Creating Value Stream Maps
Value Stream Mapping (VSM) is an indispensable tool in process optimization, and selecting the right methodology—whether traditional or digital—can significantly impact its effectiveness. While manual mapping techniques remain relevant, modern software solutions offer advanced capabilities that enhance precision, collaboration, and real-time analysis.
9.1 Traditional vs. Digital Approaches to VSM
The choice between traditional and digital VSM methods depends on factors such as organizational needs, complexity, and resource availability.
- Traditional Approach (Manual Mapping) – This method involves using whiteboards, sticky notes, or paper-based flowcharts to construct value stream maps. It allows teams to collaborate in a hands-on manner, fostering engagement and immediate feedback. However, manual mapping can be time-consuming, difficult to modify, and prone to errors in complex systems.
- Digital Approach (Software-Based Mapping) – Digital tools facilitate dynamic mapping, real-time updates, and seamless integration with other lean methodologies. They enable automated calculations, better data visualization, and the ability to simulate future-state scenarios with precision. While software solutions require an initial learning curve and investment, they significantly enhance efficiency and accuracy.
9.2 Recommended Software for Efficient Value Stream Mapping
Several software applications are tailored for Value Stream Mapping, each offering unique features that streamline the mapping and analysis process:
- Microsoft Visio – A widely used diagramming tool with built-in VSM templates that allow users to create detailed and customizable process maps.
- Lucidchart – A cloud-based tool offering intuitive drag-and-drop functionality, real-time collaboration, and seamless integration with productivity software.
- Lean Metrics by Minitab – A data-driven solution that integrates statistical analysis with VSM, providing deeper insights into process inefficiencies.
- iGrafx – A business process modeling tool that enables VSM with advanced simulation capabilities for predictive analysis.
- EdrawMax – A versatile mapping tool that provides industry-specific templates for lean manufacturing and process improvement initiatives.
10. Case Study: A Real-World Example of Value Stream Mapping
Examining real-world applications of Value Stream Mapping provides valuable insights into its transformative potential. The following case study illustrates how a manufacturing plant leveraged VSM to reduce lead time and enhance operational efficiency.
10.1 How a Manufacturing Plant Reduced Lead Time Using VSM
A mid-sized automotive components manufacturer faced persistent inefficiencies in its production line, resulting in excessive lead times, high defect rates, and inventory imbalances. The company initiated a Value Stream Mapping project to diagnose bottlenecks and streamline workflows.
Challenges Identified:
- Excessive work-in-progress (WIP) inventory, leading to increased storage costs.
- Frequent machine downtime due to uncoordinated maintenance schedules.
- Redundant manual inspection steps that delayed product flow.
- Inconsistent information exchange between production and supply chain teams.
VSM Implementation:
- A cross-functional team mapped the current-state value stream, detailing each production stage from raw material intake to finished goods dispatch.
- Data analysis revealed that 35% of total lead time was attributed to non-value-adding activities.
- A future-state map was designed, introducing lean interventions such as Just-in-Time inventory management, predictive maintenance scheduling, and automated quality inspections.
- An implementation roadmap was developed, prioritizing process enhancements and workforce training.
Results Achieved:
- Lead time was reduced by 40%, enhancing customer order fulfillment.
- Inventory holding costs decreased by 30% through optimized stock levels.
- Production efficiency improved, leading to a 20% reduction in defects.
10.2 Lessons Learned and Key Takeaways
The case study underscores several critical lessons:
- Cross-functional collaboration is essential – Engaging stakeholders from production, quality control, and logistics fosters comprehensive problem-solving.
- Data accuracy drives impactful decisions – Precise data collection and analysis ensure that VSM efforts are based on factual inefficiencies rather than assumptions.
- Continuous monitoring sustains improvements – Process enhancements must be revisited periodically to prevent the recurrence of inefficiencies.
11. The Relationship Between VSM and Other Lean Tools
Value Stream Mapping does not function in isolation; rather, it complements and integrates with other lean methodologies to drive holistic process improvements.
11.1 How VSM Complements 5S, Kaizen, and Six Sigma
- 5S (Sort, Set in Order, Shine, Standardize, Sustain) – VSM identifies inefficiencies that 5S principles can address, such as reducing workspace clutter and optimizing tool placement.
- Kaizen (Continuous Improvement) – While VSM highlights bottlenecks, Kaizen fosters a culture of ongoing enhancements, ensuring incremental improvements are sustained.
- Six Sigma – VSM provides a visual representation of process variations, while Six Sigma employs statistical methods to reduce defects and variability. Integrating both approaches enhances process reliability and quality control.
11.2 Integrating VSM with Continuous Improvement Strategies
To maximize its effectiveness, VSM must be embedded within a structured continuous improvement framework. This involves:
- Establishing Key Performance Indicators (KPIs) to monitor process efficiency post-VSM implementation.
- Conducting regular audits to assess the effectiveness of mapped improvements.
- Encouraging employee involvement to sustain a culture of proactive problem-solving.
12. Challenges in Implementing Value Stream Mapping
Despite its effectiveness, implementing Value Stream Mapping poses several challenges that organizations must proactively address.
12.1 Overcoming Resistance to Change in Organizations
One of the primary obstacles in adopting VSM is resistance to change, often stemming from entrenched work habits, fear of job displacement, or skepticism about new methodologies. Strategies to mitigate resistance include:
- Leadership Endorsement – When management actively supports VSM initiatives, it fosters organizational buy-in.
- Inclusive Decision-Making – Involving employees in the mapping process ensures that concerns are addressed and solutions are collectively developed.
- Effective Communication – Demonstrating the benefits of VSM through real-world examples and case studies helps alleviate apprehension.
12.2 Ensuring Accuracy in Data Collection and Analysis
The effectiveness of a Value Stream Map hinges on the accuracy of collected data. Common pitfalls include incomplete data sets, reliance on anecdotal observations, and failure to consider process variability. Best practices for ensuring data integrity include:
- Utilizing real-time data tracking tools – Digital monitoring systems enhance data precision.
- Standardizing data collection methods – Consistent measurement techniques improve comparability across process stages.
- Verifying data through cross-functional reviews – Engaging multiple stakeholders ensures a comprehensive and validated analysis.
13. Advanced VSM Techniques for More Effective Mapping
Value Stream Mapping (VSM) has long been a cornerstone of lean methodologies in manufacturing. However, its application extends far beyond traditional production environments. Advanced VSM techniques allow organizations to refine their mapping strategies, applying them to service-based industries and administrative workflows. These expansions enable businesses to identify inefficiencies, reduce waste, and enhance customer value across a broader spectrum of operations.
13.1 Using VSM for Service-Based Industries
While VSM originated in manufacturing, its principles are equally applicable to service industries, where the emphasis is on optimizing workflows, minimizing delays, and enhancing customer experiences. In sectors such as healthcare, finance, and logistics, service value streams contain numerous non-value-adding steps that hinder efficiency.
For example, in healthcare, patient flow from admission to discharge can be mapped to identify bottlenecks in diagnostic procedures, resource allocation, and administrative processing. VSM helps hospitals streamline operations by reducing patient wait times, optimizing staff scheduling, and improving communication between departments.
In financial services, processes such as loan approvals, insurance claims, and customer onboarding involve multiple handoffs and extensive documentation. By applying VSM, institutions can uncover redundant verification steps, automate approvals where possible, and standardize document workflows, thereby reducing lead times and improving customer satisfaction.
13.2 Extending VSM Beyond the Shop Floor to Administrative Processes
Administrative and support functions often harbor inefficiencies that remain unnoticed. Excessive paperwork, redundant approvals, misaligned communication channels, and siloed decision-making structures contribute to operational delays and resource wastage. By extending VSM to these areas, organizations can enhance productivity and responsiveness.
Common administrative applications of VSM include:
- Procurement and Supply Chain Management – Mapping supplier interactions, order processing times, and material lead times to reduce procurement cycle durations.
- Human Resources (HR) Processes – Streamlining recruitment, onboarding, and performance appraisal workflows to minimize delays in hiring and employee integration.
- Customer Service Operations – Identifying bottlenecks in query resolution and complaint handling to improve service responsiveness.
The key to successful administrative VSM lies in recognizing that information flow is just as critical as material flow. Digital tools can assist in tracking task dependencies, measuring process lead times, and visualizing workflow inefficiencies to drive structured improvements.
14. The Future of Value Stream Mapping
As industries embrace digital transformation, Value Stream Mapping is undergoing a paradigm shift. The incorporation of artificial intelligence, machine learning, and real-time analytics is reshaping traditional mapping techniques, making them more dynamic and predictive.
14.1 Emerging Trends in Digital and AI-Powered VSM
The integration of digital tools has significantly enhanced the accuracy and effectiveness of Value Stream Mapping. Key advancements include:
- AI-Driven Process Analysis – Machine learning algorithms can automatically analyze workflow data, identifying hidden inefficiencies and predicting future performance trends.
- Real-Time Data Synchronization – IoT-enabled sensors and enterprise resource planning (ERP) systems can feed live data into VSM models, allowing for dynamic updates and scenario simulations.
- Automated Process Mining – AI-based software can extract workflow data from digital logs, eliminating the need for manual mapping and enabling continuous improvement cycles.
These advancements enable organizations to shift from static, periodic mapping exercises to real-time, adaptive process optimization. Instead of revisiting VSM at fixed intervals, businesses can implement a continuous feedback loop where inefficiencies are detected and addressed proactively.
14.2 How VSM Continues to Evolve in the Era of Industry 4.0
Industry 4.0—characterized by automation, interconnected systems, and data-driven decision-making—has redefined the application of VSM. Traditional paper-based mapping is giving way to cloud-based, interactive platforms that facilitate cross-functional collaboration.
In smart factories, VSM is integrated with cyber-physical systems to monitor material flows, machine utilization, and workforce efficiency in real-time. Predictive maintenance strategies, guided by VSM insights, help reduce unplanned downtime and optimize resource allocation.
15. Conclusion
Value Stream Mapping remains one of the most powerful tools for visualizing and optimizing workflows, whether in manufacturing, services, or administrative processes. Its ability to highlight inefficiencies and drive structured improvements makes it an essential practice in lean management.
15.1 Key Takeaways and Final Thoughts
- VSM is no longer limited to manufacturing; its application in service industries and administrative functions is growing.
- Advanced VSM techniques, particularly in digital and AI-driven environments, provide deeper insights and real-time optimization capabilities.
- The future of VSM lies in integration with Industry 4.0 technologies, making process analysis more dynamic and predictive.
To sustain this culture:
- Leadership should actively support and promote VSM initiatives.
- Employees should be trained in VSM methodologies to enable widespread participation.
- Mapping exercises should be conducted regularly, evolving with business needs.
By making Value Stream Mapping an integral part of strategic planning and operational refinement, organizations can achieve sustained efficiency gains, reduced waste, and enhanced value delivery to customers.